When it comes to choosing the right material for cutting tools in CNC machining, tool steel stands out. Its unique properties, like high hardness and resistance to wear and bending, make it ideal for shaping materials through cutting and machining.
But what are the various grades of tool steel, and how do you select the best one for your machining needs?
This article discussed tool steel, covering its nature and detailing the main types of tool steel, along with their characteristics, compositions, and applications.
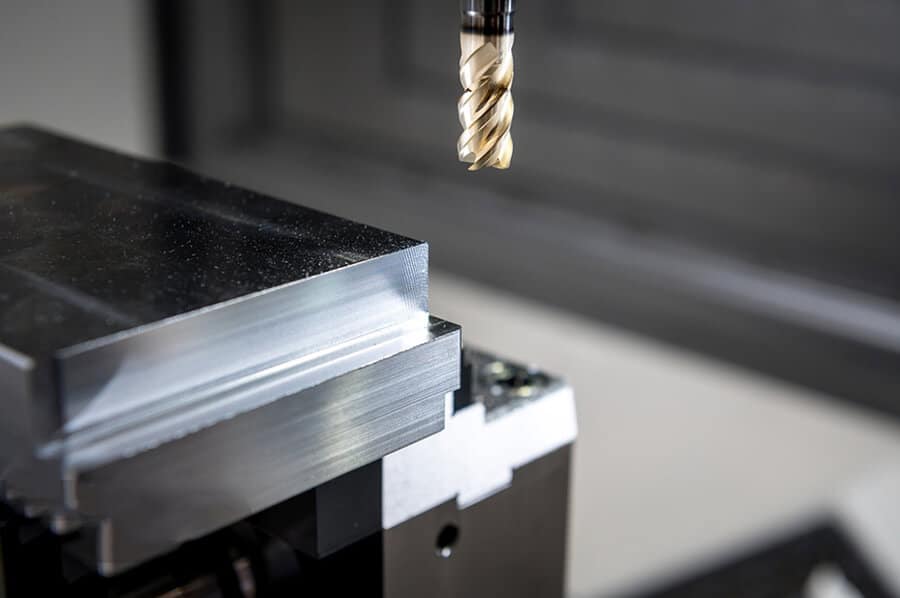
What is Tool Steel?
Tool steel refers to different types of strong carbon and alloy steels that are especially suitable for making tools like reamers, drills, machine dies, and hand tools since they are very hard, resistant to wearing down and deformation, and can keep a sharp edge even when subjected to elevated temperatures.
For instance, high-speed steels have specific carbide-forming elements like chromium, vanadium, molybdenum, and tungsten, which are very hard compounds. They also perform well at high temperatures, especially when cobalt or nickel is added. Tool steels are often heat treated to make them even harder and are used for tasks like metal stamping, shaping, forming, cutting, and plastic forming.
What are the Compositions of Tool Steel?
Tool steels are made up of different mixtures of metals like chromium, molybdenum, tungsten, and vanadium. These are alloys based on iron with plenty of carbon for strength and forming hard carbides.
Nickel and cobalt are added to make the steel strong at high temperatures. Chromium, molybdenum, tungsten, and vanadium are also added to make the steel hard and resistant to wear.
Tool steels are sorted into groups based on what they’re made of and how they behave. These groups generally include carbon tool steel, alloy tool steel, and high speed steel.
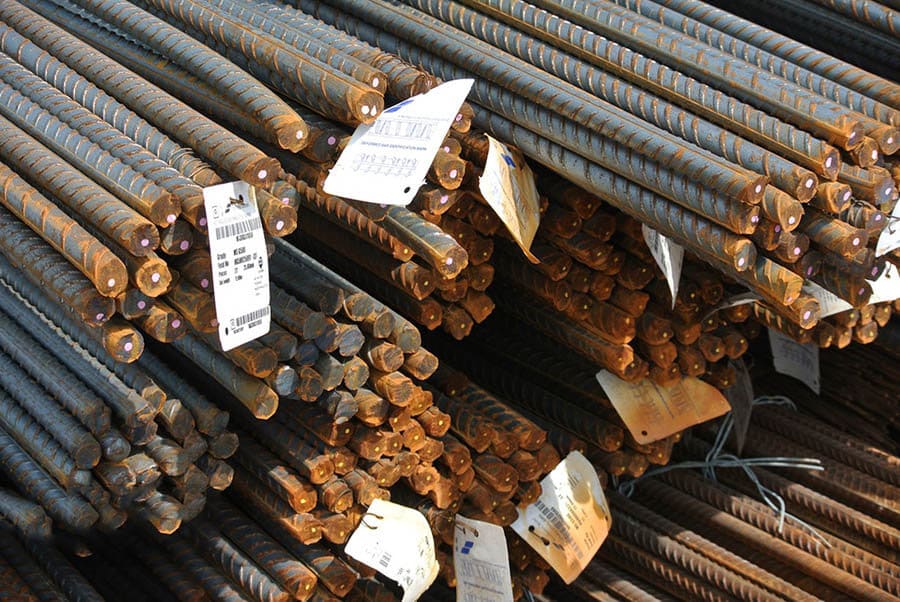
What are the Main Types of Tool Steel? – Classifications of Tool Steel
Tool steels come in seven main types: water-hardening, hot-work, cold-work, shock-resisting, plastic mold, high-speed, and special purpose tool steel. The table below shows these types along with their corresponding AISI-SAE designation, subcategories, and characteristics:
Categories of Too Steel | AISI-SAE Grade | Subcategories and attribute |
---|---|---|
Cold-Worked | O | O1 – O7 (Oil-hardening, low carbon) |
A | A2 – A10(Air-hardening, medium alloys) | |
D | D2 – D7(High carbon, high chromium) | |
Hot-Worked | H | H1-H19(Chromium) |
H20-H39(Tungsten) | ||
H40-H59(Molybdenum) | ||
High-speed | M | M1, M7, M10(Molybdenum) |
M30, M33, M34, M42, M43, M46, M47(Molybdenum, Cobalt) | ||
M2, M3, M4(Molybdenum, Tungsten) | ||
M6, M15, M35, M36< M41, M44, M45(Molybdenum, Tungsten, Cobalt) | ||
T | T1, T2, T3, T7, T9(Tungsten) | |
T4, T5, T6, T8, T15(Tungsten, Cobalt) | ||
Special Purpose | F | F1(High carbon, low alloys) |
F2, F3(Tungsten) | ||
L | L1, L3, L7(Carbon > 0.65%, Chromium) | |
L2(Carbon <0.65%, Chromium) | ||
L6(Carbon > 0.65%, Nickel) | ||
Water-Hardening | W | W1 to W7 (High carbon) |
W1 A – 1B(Carbon) | ||
W2 – W3(Carbon, Vanadium) | ||
W4 – W5(Carbon, Chromium) | ||
W7(Carbon, Chromium, Vanadium) | ||
Plastic Mold | P | P1- P20, P21(Low carbon) |
Shock-resistant | S | S1, S3(Tungsten) |
S2, S4, S5, S6(Silicon) | ||
S7(Chromium) |
High-Speed Steels(M, T-Grade)
High-speed steels (HSS) come in two types: M-type (molybdenum-based) and T-type (tungsten-based). The molybdenum steels have a shorter hardening range and a lower hardening temperature than the tungsten grades because their melting point is somewhat lower. M-type high-speed steels are more durable although they’re slightly less hard than T-type high-speed steels. The most common steel in this category is M2 high-speed steel.
HSS can withstand high temperatures while still maintaining their hardness. They’re called high-speed steels because they can perform optimal tool speeds and feed rates compared to regular high-carbon steels. HSS grades are usually much harder and more resistant to wear than traditional carbon and tool steels, owing to the tungsten and vanadium components.
HSS are often used to make drill bits, tool bits, power-saw blades, milling cutters, router bits, and gear cutters.

Water-Hardening Tool Steels (W-Grade)
W-grade tool steels have high carbon content that needs to be quenched in water because it doesn’t harden as well as other tool steels due to their low alloy content. Small amounts of other elements like molybdenum, manganese, and silicone can be added to give the steel extra functions. It’s cheaper than other tool steels, so it’s commonly used for basic applications.
While it’s cost-saving than other types of tool steels, it can’t endure high temperatures — it starts to soften at 150°C. This steel can become very hard but it’s more likely to break than other kinds of tool steels. Water quenching is a must for all W-grade tool steels but it can lead to more warping and cracking.
This type of tool steel is commonly used for making razor blades, cold heading dies, lathe tools, embossing tools, reamers, and industrial cutting tools.
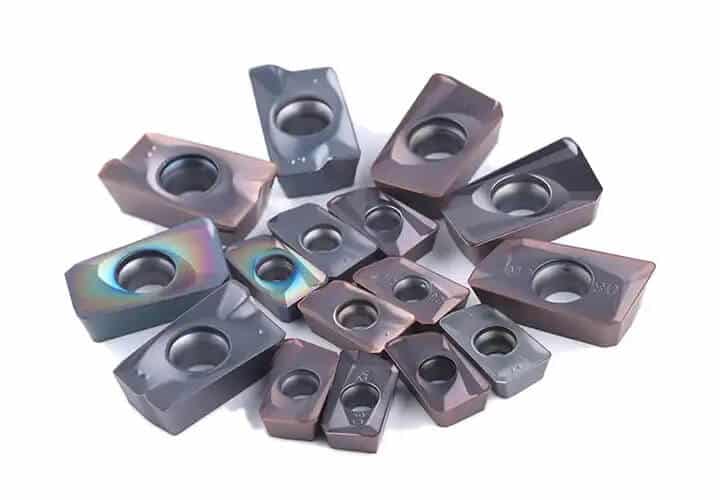
Cold-Work Tool Steels(A, O, D-Grade)
Cold-work tool steels are known for their medium hardness, strong resistance to wear, and the ability to harden easily. They’re usually used to make bigger parts or parts that need to remain the same shape even after hardening. These tool steels are categorized into three groups: air-hardening (A-grade), oil-hardening (O-grade), and high-carbon chromium (D-grade) tool steels.
Air Hardening or A-Grade Tool Steel
These tool steels have good hardening abilities and a low hardening temperature range like oil hardening grades. A6 tool steel has less distortion compared to other air-hardening or oil hardening grades. It’s easy to machine and has a nice mix of toughness and resistance to wear. It’s often used for coining, cams, die bending, arbors, and blanking.
Oil Hardening or O-Grade Tool Steel
This group of tool steel is quenched with oil during manufacturing. It’s used in many different jobs because of its high strength and resistance to abrasion. Oil hardening tool steel can be found in applications like master engraving rolls, thread cutting chasers, punches, bushings, and collets.
High Carbon Chromium or D-Grade Tool Steel
This cold-working tool steel is also known as high carbon chromium with 11-13% chromium. Although they can’t offer high resistance to corrosion, their 1.4-2.5% carbon content makes them good at resisting wearing down and suitable for long production runs.
Also, they can be hardened with oil or air without much distortion, making this tool steel useful for making cutters. The D series tool steel is also great for making seaming and forming rolls, plastic injection molds, lathe centers, and woodworking knives. It’s also used for burnishing tools, lamination dies, draw punches, and cold extrusion dies.
Hot-Work Tool Steels (H-Grade)
The tool steels in this group usually have a good amount of different metals but not much carbon. They can retain their qualities and work well even when they’re exposed to high temperatures for a long time, except when cutting. The most commonly used tool steel in this group is H13.
Its excellent heat resistance makes it great for making materials like metal and glass that need to be really hot to work well. It’s often used for making cold heading die casings and for hot extrusion processes with magnesium or aluminum.
In this group, the amount of different metals used determines the type of tool steel. The main alloy elements are molybdenum, tungsten, and chromium.
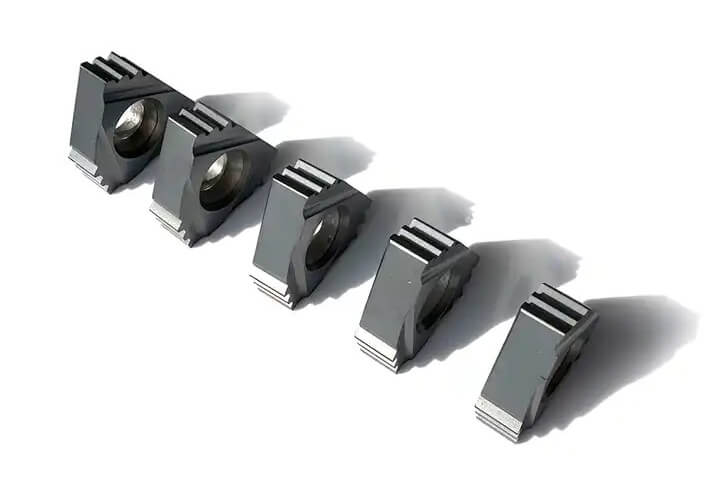
Molybdenum-based Tool Steel
This type of hot work tool steel contains a high amount of molybdenum. It offers strong resistance to wear and remains stable under high temperatures, making it suitable for extreme conditions. Additionally, its ability to withstand force and heat also makes it suitable for use in metal mills as cutters or dies.
Tungsten-based Tool Steel
This kind of tool steel has 9-18% tungsten and 2-4% chromium. While it’s brittle, it’s really good at resisting heat. To avoid its brittleness, you can preheat it to the right temperature before using it.
Chromium-based Tool Steel
The chromium type is the most commonly used hot work tool with 3-5% chromium content. It may also have less than 5% of other alloying elements such as molybdenum, tungsten, or vanadium. This type of tool steel is often used for plastic injection mold making, hot forging, and hot working punches.
Shock-Resisting Tool Steels (S-Grade)
Shock-resisting tool steel is designed to handle stress at low temperatures and has decent hot hardness. The S-grade tool steels are known for their strong impact toughness but don’t resist abrasion very well. They can’t handle high heat and have a limit of 537°C.
S-grade tool steels are used for things like blacksmith chisels, boiler shop tools, tool chuck jaws, collets, clutch parts, jackhammer parts, hot and cold swaging dies, hot and cold shearing blades, and chipper knives.
They’re also used in pneumatic tools, hot stamps, chipper knives, cold and hot working chisels, hot forming dies, and cold gripper dies. The S7 tool steel is the most popular in this group.
Mold Steels (P-Grade)
P-grade tool steels are used to create mold steels for plastic parts making. They are well suited for making molds and dies for processes like cold punching, hot forging, die casting, and plastic injection molding. Common grades of mold tool steel include P20 and 420 (highly refined, high-quality stainless steel for molds).
Mold steels have a great integration of toughness, corrosion resistance, hardness, and the ability to withstand wear and tear. Additionally, tool steels in this category also have high impact strength and are easy to polish.
Special Purpose Tool Steels(F, L-Grade)
Special purpose tool steels are more costly than general W-grade tool steels. They have special compositions and qualities that make them ideal for specific uses that regular W steels can’t handle. These steels don’t require the additional cost of other tool steel alloy content and are free from the difficulties of heat treatment.
Special purpose tool steels are categorized into two groups: low alloy (L-type) and carbon-tungsten-based (F-type).
- L-type tool steels are useful for applications where toughness and wear resistance are essential. They’re ideal for making bearings, clutch plates, rollers, wrenches, cams, and collets. Steels in this group with more carbon content are used for dies, drills, gauges, knurls, and taps.
- F-type tool steels are hardened with water and are much more wear resistant than W-type tool steel. These steels are good for uses that need high wear resistance but not high temperature or shock resistance, such as paper-cutting knives, broaches, burnishing tools, reamers, and plug gauges.
How is Tool Steel Made?
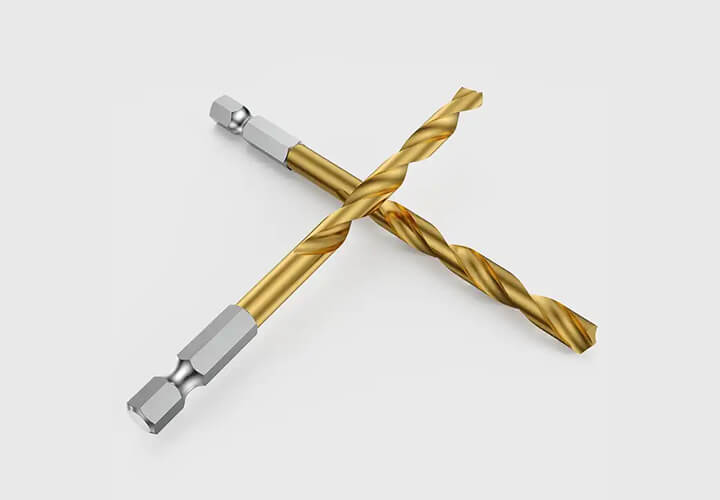
There are various ways to make tool steel. These methods include electroslag refining (ESR), electric arc furnace (EAF), powder metallurgy, primary melting, primary breakdown, rolling, hot and cold drawing, continuous casting, and osprey process.
Here are some main methods:
Electric Arc Furnace (EAF)
The Electric Arc Furnace (EAF) process involves melting recycled steel scrap in an electric arc furnace along with alloying components. To prevent oxidation, the molten mixture is treated with chemicals and poured into a large ladle. After impurities are removed during the refining stage, the steel can be poured into large molds to form ingots.
Electroslag Refining (ESR)
Electroslag Refining (ESR) is an alternative to EAF. This method uses a progressive melting process to produce ingots with smooth surfaces and no holes or imperfections, resulting in high-quality steel with minimal flaws.
Powder Metallurgy
Powder metallurgy is a more advanced method that involves using powdered metal to create tool steel with enhanced hardening and machinability. This process is particularly effective for producing tool steel with higher levels of carbon and alloying materials needed for applications like aerospace components.
Common steps involved in manufacturing tool steel include:
- Annealing: This process involves heating the steel to a specific temperature and holding it there for a set duration before cooling it down. This helps alter the steel’s molecular structure, making it less brittle and more workable.
- Hot or Cold Drawing: Drawing processes are employed to attain tighter tolerances, smaller sizes, or distinctive shapes with tool steel. Due to the high strength and limited ductility of tool steels, multiple passes or hot drawings at temperatures up to 540 °C are utilized. Cold drawing is usually limited to a single, light pass to prevent breakage of the feedstock.
What are the Properties of Tool Steel?
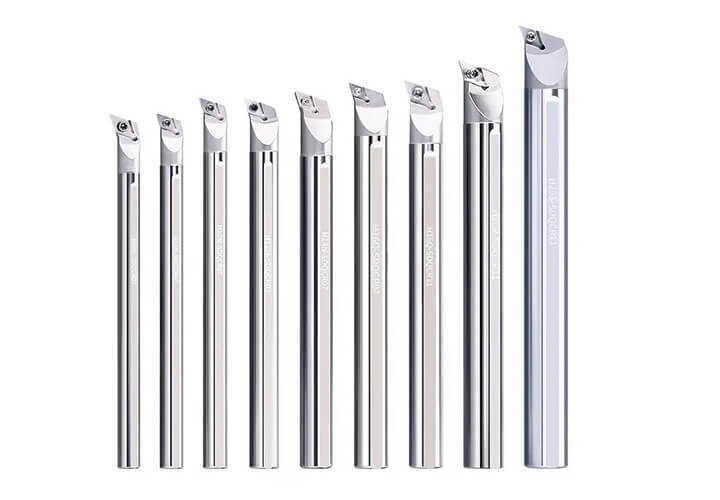
The key properties of tool steel are wear and heat resistance and toughness. Alloying elements are added to increase strength, wear resistance, hardness, and toughness. Hardness measures the degree of resistance to deformation of steel. The Rockwell C test is commonly used to determine the hardness of tool steels. Hardened cold work tool steels typically have a hardness of around 58/64 HRC (Rockwell C), with most falling between 60/62 HRC, and some occasionally used up to 66 HRC, depending on the grade.
The table below shows the most common tool steels and their comparative properties.
Grades | Properties |
O1 | Oil-hardening Easy to machine Good abrasion resistance Optimal hardness response at low temperatures High dimensional stability during hardening A maximum HRC of 65 |
W1 | Water-hardening Excellent wear resistance Good toughness A maximum HRC of 68 |
A2 | Air-hardening Higher heat resistance and wear resistance than O1 High dimensional stability A maximum HRC of 63, with fewer distortions |
D2 | High carbon and high chromeIdeal grade for maximum production runs Excellent toughness and wear resistance High compressive strength A maximum HRC of 65 |
S7 | Shock-resistant tool steel High strength and ductility Used for moderately elevated temperature service A maximum HRC of 61 |
P20 | Special-purpose tool steel Ideal for machining die-casting components and plastic molds A maximum HRC of 32 |
H13 | Hot-worked High resistance to thermal fatigue cracking High hardenability Good wear resistance Excellent toughness A maximum HRC of 54 |
M2 | High-speed Excellent abrasion resistance Good toughness A maximum HRC of 65 |
What Should You Consider When Choosing A Tool Steel Grade for Machining?
The specific tool or product you plan to machine greatly influences the types of tool steel you should select. Additionally, different steel grades and types possess distinct properties that render them suitable for various applications and purposes. As such, when selecting a grade for your machining needs, certain factors should be taken into account.
Properties of Tool Steels
A wide variety of tool steel types exist for metal machining, each varying in properties such as chemical composition, toughness, and strength.
Toughness
The toughness of tool steel refers to its ability to resist breakage, chipping, or cracking under stress or impact. If toughness were the sole factor in choosing tool steel, H13 or S7 would be the obvious choice. However, it’s essential to consider all desired characteristics and the specific job requirements when making your selection.
As the alloy content increases, the toughness of tool steel tends to decrease. Additionally, the manufacturing process of the steel also influences its toughness. The PM (particle metallurgy) production process can improve the toughness of the steel grade because of the uniformity of its microstructure.
The hardness of tool steel also impacts its toughness. Generally, a given grade of tool steel will exhibit better toughness at a lower hardness. However, lower hardness could negatively affect other essential characteristics required for achieving acceptable tool life.
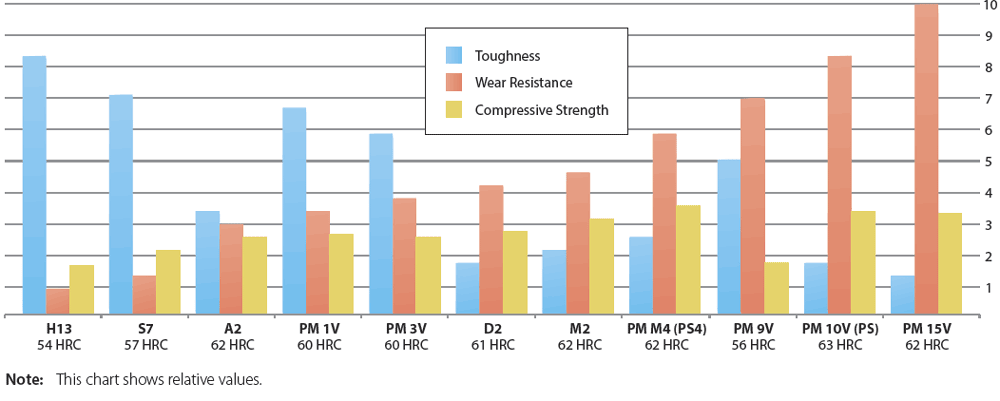
Wear Resistance
Wear resistance refers to how well the tool steel can withstand being worn away or eroded by contact with the work material, other tools, or external factors like scale and grit.
There are two types of wear damage in tool steels: abrasive wear, which involves the cutting edge being worn down, and adhesive wear, where the workpiece material sticks to the punch point, decreasing the friction coefficient and increasing the perforating pressure.
Increased alloy content generally means higher wear resistance due to the increased presence of carbides in the steel. Carbides are tough particles that enhance wear resistance. They are formed when alloys like vanadium, tungsten, molybdenum, and chromium combine with carbon as the molten steel solidifies. While increased carbide amounts improve wear resistance, they also decrease toughness.
Compressive Strength
Compressive strength is an important feature of tool steels but it’s somewhat overlooked. It measures how much force an item can handle before it deforms or breaks.
There are two things relevant to compressive strength: the amount of alloy in the steel and how hard the tool steel is. Elements like Molybdenum and Tungsten add to the compressive strength, and higher hardness also makes the compressive strength better.
Machining Speed
Some tool steels may not function well at high speeds. If you use the wrong grade for high-speed machining, the tool steel could lose hardness and wear resistance over time. When working at high speeds, it’s best to use high-speed steel because it offers greater resistance to wear and extreme temperatures, even at high speeds.
Cost
Price is a key factor to think about when selecting a tool steel grade for CNC machining toolings or CNC steel machining. It’s best to avoid skimping on the material choice because a premature tool failure could end up costing more.
Before settling on a specific tool steel grade for machining, it’s a good idea to do a cost-benefit analysis. This will make sure that the chosen material is suitable for delivering the needed performance.
FAQs
Conclusion
Tool steel is a type of carbon alloy used in various applications, grouped into different categories based on the percentage of other alloying elements, quenching type, and temperature range. Selecting the appropriate tool steel grades for your project can significantly impact its success. Therefore, it’s crucial to understand the various types of tool steels, how they are hardened, and the unique properties that make them suitable for different applications and purposes.
Custom Precision CNC Machining Tool Steel Parts at Runsom Precision
If you’re unsure about which tool steel grade is best for your product, don’t worry. Our team of professionals and engineers is here to help you choose the right steel materials for the finest outcomes.
As a trusted and well-known manufacturer, Runsom Precision offers comprehensive manufacturing services like CNC machining, 3D printing, rapid prototyping, and surface finishing. Whether you need tool steel machining or steel molding services, we can fulfill all your requirements. Reach out to us to get an instant quote for top-quality tool steel metal products for your next project.
Other Articles You May Be Interested in: