歯車 何世紀にもわたって存続しており、最も古いものの、今日でも適切な機械要素の 1 つとなっています。
さまざまな方法を含む 鋳造、鍛造、押出、粉末冶金、ブランキング、および歯車フライス加工を使用して歯車を作成できます。歯車の製造には単一の工程はなく、種類や用途に応じて異なる工程が必要となります。しかし、最終的な歯車のサイズ、形状、形状を実現するには、機械加工プロセスが非常に重要です。 表面仕上げ.
このガイドでは、一般的なプロセス、後処理操作、材料について説明し、歯車の製造について説明します。

歯車製造とは何ですか?
歯車の製造工程では、伝達する機械に欠かせない部品である歯車を精密に製造、成形します。 トルク。回転運動で知られる歯車には、別の歯付き機構の歯と噛み合う歯があり、機械的動力のスムーズな伝達を可能にします。
歯車の製作には、機械加工、粉末冶金、鋳造、プレス加工などさまざまな方法があります。歯車のフライス加工、ブローチ加工、ホブリングは、複雑で明確な歯車プロファイルを実現するために使用される最も正確で一般的な技術の 1 つです。これらの方法により、機械のさまざまな用途に必要な歯車を正確に製造できます。
歯車の製造には、金属、プラスチック、さらには木材などのさまざまな材料が使用されます。技術の進歩により、金属やプラスチックの歯車を形成できるようになりました。 ダイカスト また 射出成形、代替製造方法を提供します。これにより、メーカーは従来の歯車製造を超えた選択肢を模索できるようになります。それにもかかわらず、最終歯車製品の品質を向上させるために後処理作業が必要な場合があることを認識することが重要です。

典型的な歯車の製造プロセス
歯車の製造方法は、通常、生成、成形、形状切断の 3 つの主要なカテゴリに分類されます。
- 歯車成形では、切削工具を使用せずに歯車を作成します (鋳造、鍛造、粉末冶金、3D プリントなど)。
- 歯車形状の切削には、歯車プロファイルの作成に使用される工具 (つまり、歯車フライス加工、ブローチ加工、EDM) が必要です。
- 歯車生成では、目的の歯車プロファイルの形状の切削工具を使用して歯車を作成します (つまり、歯車の成形と歯車のホブ加工)。
ギアフォーミング
鋳造
鋳造は、溶かした金属を型のキャビティに注入して形状を作成する成形プロセスです。これは主に歯車のブランクまたはシリンダーを製造するために使用される比較的単純なプロセスであり、歯は通常機械加工によって作成されます。
しかし、鋳造が業界で優先される製造方法として君臨する特定の分野、つまり非常に大きな歯車の製造が存在します。機械加工法やその他の歯車形成技術は、直径が大きい場合には実用的ではありません。通常、大型の歯車は主に平歯車タイプであり、比較的単純な鋳造が優れた選択肢としてさらに確立されています。
シェル鋳造、 ダイカスト、 砂型鋳造、 と 永久鋳型鋳造 歯車の製造に使用される最も一般的なタイプの鋳造方法です。

鍛造
このプロセスでは、特定の要件に基づいてブランクと完成したギアの両方を柔軟に製造できます。鍛造は、比較的単純な歯車に特に適しています。
理論的には、単純な理論的根拠により、鍛造は重負荷用途に最適な歯車製造方法です。鍛造に伴う熱処理により、ギアの疲労特性が向上します。しかし、鍛造には大きな力が必要となるため、製造される歯車のサイズや薄さに制限が生じます。
通常、鍛造は直径 6 ~ 10 フィートの範囲の歯車に効果的です。精密鍛造などの鍛造の種類によっては、最終歯車製品に機械加工が必要な場合と不要な場合があります。

積層造形
積層造形、一般的に呼ばれる 3Dプリントは、CAD 3D モデルに基づいて 3 次元オブジェクトをレイヤーごとに構築することによって動作します。このアプローチにより、積層機械は、質量を削減するように設計された格子構造を組み込んだ複雑なデザインを作成することができます。これは、従来の方法では簡単に達成することができなかった偉業です。このようなジオメトリの作成には、多くの場合、 3Dトポロジ 最適化とジェネレーティブ コンピューター デザイン。
積層造形プロセスを利用して、従来の非円形歯車を製造できます。さらに、高品質の 3D プリンターは現在、手頃な価格で簡単に入手できるようになりました。
粉末冶金
粉末冶金 これは、従来の機械仕上げの鋼および鋳鉄ギアに代わるコスト効率の高い高精度成形方法として機能します。ただし、大きな歯車サイズには適さず、小型で高品質な歯車を作ることに優れています。 拍車, ベベル、スパイラルギア。
大きな歯車では材料の多孔性が低下し、疲労と耐衝撃性が低下し、耐荷重能力が制限されます。それにもかかわらず、焼結プロセスを採用すると、機械的特性を向上させることができます。
この方法は、穴、くぼみ、さまざまな表面レベルや突起などの特徴を組み込んだ歯車の設計に有利であることが証明されています。これらの利点にもかかわらず、粉末冶金の初期設定コストはかなり高く、少量生産には非現実的です。

ブランキング
ブランキングは押し出しと同様、多くの類似点がありますが、3 次元機能に制限があります。この歯車形成方法では、板金と複数の金型を使用して目的の形状を実現します。ブランキングプロセスを使用してさまざまなタイプの歯車を製造できますが、平歯車は最適な結果をもたらします。
現在、ブランキングプロセスは、特に軽量用途において、複数の業界にわたる歯車製造に応用されています。これらには、オフィス機器、油圧機器、小型医療機器、および負荷要求が比較的低いその他のアプリケーションが含まれます。
ギヤフォームカット
フライス加工
歯車フライス加工には、形状切削工具を使用することが含まれます。 製粉機 ギアブランクからギア歯を削り出します。この基本的な機械加工プロセスは、回転するマルチエッジ カッターとワークピースの間の動きに依存して、個々の歯車の歯を成形します。
ミーリングフォーム切断方法は用途が多少制限されていますが、複雑な歯車形状の作成に優れており、特別な工具を必要とせずにカスタム切断を実行できます。
CNC フライス加工は、ホブ カッターだけでなく、自動車トランスミッションなどのさまざまな産業向けのヘリカル ギヤ ホイールや平歯車ホイールを製造するために一般的に使用されています。

ブローチ加工
ブローチ加工は、歯車の形状を切断するための最も迅速な技術の 1 つとして際立っています。ブローチとして知られる複数の歯を持つ切削工具が使用され、各歯は通常、前の歯よりも高くなっています。この段階的な高さの変化により、より小さく簡単なカットの作成が容易になり、精度を犠牲にすることなく目的の形状を迅速に得ることができます。
この歯車の製造方法は一般に内歯車と関連付けられていますが、外歯の作成にも適しています。これを実現するには、「」に特化したツールが必要です。ポットブローチ加工」が利用され、同じレベルの精度と効率の複製が保証されます。
放電加工 (EDM)
EDM は、誘電体バス液によって分割された 2 つの電極間で一連の電流放電を引き起こすことにより、ワークピースから材料を除去する電気機械製造技術を表します。火花は切断するのではなく、本質的に材料を侵食する「切断ツール」として機能します。
EDM は、歯車切断プロセスなど、あらゆるサイズの複雑な形状の切断に優れています。ただし、この方法には欠点もあります。正確な制御とプログラミングがないと、部品の表面が損傷する可能性があり、CNC プログラムで湾曲した歯のプロファイルを実行する場合は特に困難です。それにもかかわらず、高品質でユーザーフレンドリーなアプリケーション 3Dモデリング また、Feature CAM、Autodesk Fusion、Master CAM などの CAM ソフトウェアを使用すると、湾曲した歯を切削するために必要なスムーズな動作を容易にすることができます。
近年、EDM 機械は改良され、表面仕上げに関する問題が減少し、切断精度とその結果得られる材料特性 (微細構造、機械的特性など) が向上しました。このプロセスでは、1,000 分の 1 インチという厳しい公差を実現し、小さな歯車 (直径が 1 インチの数分の 1 インチ) と大きな歯車 (直径 20 インチを超える) の両方を製造できます。 EDM は、時計や時計の繊細な用途や、レースカーで使用されるものなどの頑丈なギアの切断に使用されます。

歯車の生成
歯車ホブ加工
歯車のホブ切りのプロセスには、ホブとして知られる円錐形の切断装置が使用され、ホブが歯車のブランクの周りを回転すると、ホブとワークピースの両方が回転します。
主に平歯車がこの方法で製造されていますが、サイクロイド歯車など他のさまざまな歯車もこの方法で製造されています。 はすば歯車, ウォームギア、ラチェット、および スプロケット、すべてホブ加工によって製造されます。ホブの品質は、特に複雑な形状を切断する場合に最も重要です。
歯車のホブ切り加工は、一般的に内歯車には適していません。ギアの成形と同様に、ホブ加工にはセットアップ上の利点がありますが、ホブはギアのブランクの外側を彫刻するため、外側の切断に限定されます。

ギアの成形
歯車の成形プロセスには、目的の歯の形状に一致するプロファイルを備えたカッターが必要です。この切削工具は、直線運動を利用してギアブランクから材料を除去し、切削と戻りのストロークで構成されます。歯車成形ツールのピッチは歯車の歯に必要なピッチと一致しており、さまざまな歯数の歯車に対応します。
歯車成形は、中規模の生産工程に実行可能なソリューションであることが証明されており、大量生産における速度、設計、セットアップの利点が得られ、ウォーム ギアと内歯車を除くほとんどの歯車タイプの作成が容易になります。ただし、歯車成形の欠点は、カッティング アームの剛性が限られているため、精度が低下することです。
サンダーランド法
一次歯車の製造技術の中で、ラック式カッターが重要な役割を果たしています。サンダーランド法またはサンダーランドシステムとも呼ばれるギアラック切断のプロセスには、すくい角と逃げ角を備えたラックカッターを備えた歯車機械を使用して、ギアブランクの歯形を成形します。この方法は、ラックとピニオンと同様に、加工中のワークピースとカッター間の特定の相対運動に依存します。
サンダーランド工法は均一な歯形を作ることに優れており、同じカッターで切った歯車は理論上正しく噛み合います。その結果、二重はすば歯車をはじめとする高精度が要求される歯車設計を効率的に製造することができます。さらに、サンダーランド法は、特に中量から大量の生産において多用途性と費用効果が高いことが証明されています。
歯車製造の後処理
上記で詳述した歯車の製造プロセスが完了すると、歯車の表面仕上げと寸法精度が特定の用途の特定の要件を満たさない場合があります。したがって、一連の仕上げ作業が必要となる。これらの後処理作業には、疲労特性を向上させるための熱処理、寸法修正、表面仕上げなどのさまざまな処理が含まれます。
ここでは、歯車の製造で頻繁に使用される 5 つの最も一般的な表面仕上げプロセスを紹介します。
- 研削: このよく知られた表面仕上げプロセスは、名前が示すように、表面全体に効果的に滑らかな仕上げを提供します。結果に影響を与えることなく、断続的または連続的に実行できます。
- ラッピング: 最高の精度を必要とする繊細な歯車に適したラッピングでは、小さな砥粒を使用して低速または中速で表面を入念に滑らかにします。
- ホーニング: もう 1 つの広く使用されているプロセスであるホーニングは、表面を研磨して滑らかな質感を与えると同時に、歯の形状の小さな誤差を修正します。
- シェービング: 滑らかなプロファイルを得るために表面から非常に薄い層を除去することを伴うシェービングは、比較的コストのかかるプロセスであり、歯車の製造ではあまり利用されません。
- バニシング: この技術には、圧縮を利用して表面を磨き、本質的に滑らかにすることが含まれます。
歯車の製造に利用できる材料
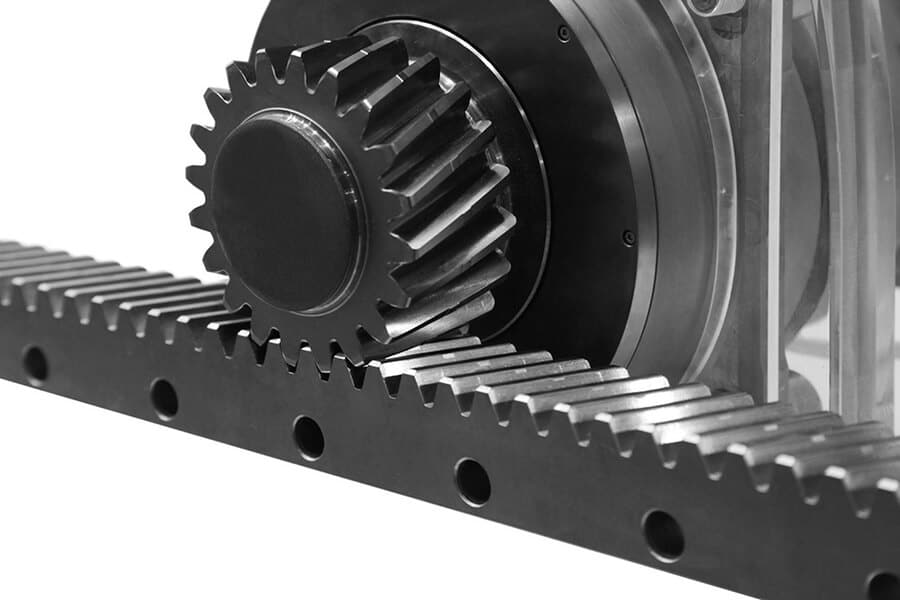
信頼性の高い性能と寿命の延長のために、ギアは次のような特定の特性を備えている必要があります。
- 低摩擦係数
- 優れた製造性
- 静荷重に耐える高い引張強度
- 負荷変動に耐える高い耐久性
これらの重要な特性を与えるために、歯車の製造には数多くの材料が使用されています。以下に各素材の概要と特長をご紹介します。
鋳鉄
鋳鉄は繰り返しの持続的な摩耗に耐えることができるため、精密な歯車の製造に適しています。鋳造法により複雑な歯車形状を容易に製造できます。鋳鉄製ギアは、スムーズな動作が主な関心事ではない用途でよく使用されます。
鋼
合金鋼で作られたギアは、一般的に使用されるため高い強度を誇ります。 熱処理 特に歯の靭性と硬度を向上させます。特に、 炭素鋼 ヘリカルラック、スパーラック、ベベルラック、ウォームラック、ギアラックの製造に利用されます。
真鍮
銅と亜鉛を組み合わせた真鍮は、メーカーが亜鉛含有量を調整できる合金です。亜鉛濃度が低い真鍮は、他の材料に比べて延性が高く、銅ベースにより金属が抗菌性になり、機械加工が容易になります。通常、真鍮歯車は平歯車や歯車ラックなどの低負荷用途に使用されます。
ブロンズ
黄銅の他に、他の銅合金にはアルミニウム青銅やリン青銅合金も含まれます。これらの非磁性歯車は腐食環境での使用に最適です。
銅、錫、リンを組み合わせたリン青銅は、錫の存在により強度と耐食性が向上し、リンの添加により剛性と耐摩耗性が向上します。このため、リン青銅ギアは、ホイールによって生じる摩擦に効果的に耐え、潤滑の影響を最小限に抑えるため、高摩擦環境、特にウォームギアに最適です。
銅、アルミニウム、ニッケル、鉄、マンガンで構成されるアルミニウム青銅は、摩耗や腐食に対して優れた回復力を示し、塩水、酸化、腐食にさらされる腐食性の高い環境での使用に適しています。 有機酸。さらに、高負荷環境でも優れた性能を発揮するため、ウォームホイールやスクリューギアを含む用途に適しています。
アルミニウム合金
高い強度対重量比のギアが要求される設定では、アルミニウム合金が鉄合金の有力な代替品として機能します。さらに、アルミニウム合金で作られたギアは、パッシベーションと呼ばれる保護表面仕上げの恩恵を受け、腐食や酸化から保護されます。
歯車製造に使用されるアルミニウム合金は 2024 年以降に普及しています。 6061、 と 7075。グレードに関係なく、アルミニウム製ギアは約 400 °F で劣化し始めるため、低温から中程度の温度での用途に最適です。
粉末金属
これらの金属は、鉄ニッケル鋼、プレ合金鋼、カスタマイズされたブレンドなどの金属材料のさまざまな組み合わせで構成されています。さらに、その多孔性はより静かなギア動作に貢献し、さまざまなオイルの真空含浸によって自己潤滑にすることができます。
このプロセスには、次の 3 つの重要なステップが含まれます。
- 耐久性、精度、信頼性の仕様に合わせた最適な組み合わせを開発
- 正確な要件を満たすために制御された圧力下で混合物を圧縮する
- ブレンドを加熱または焼結して永久的な形状を得る
粉末冶金では、ベベル、スパイラルベベル、平歯車、ヘリカル歯車、ピニオン歯車、および組み合わせ歯車を製造できます。
熱可塑性樹脂
精密製造において、軽量ギアは次のような要素に大きく依存します。 熱可塑性プラスチック。これらの歯車は金属歯車と同様に製造できます。 射出成形 多くの場合、この方法が好まれます。アセタールは、幅広い温度範囲で安定しているため、メーカーの間で人気のある選択肢です。 摩擦係数、クリープに対する耐性。
カスタムギア製造ソリューションプロバイダー – Runsom Precision
歯車製造の高度に専門化された分野での作業には、高い精度と正確さが要求されます。機械システムにおける重要な役割のため、最も小さな製造上の欠陥でも重大な結果を引き起こす可能性があります。したがって、サービスプロバイダーを慎重に選択することをお勧めします。
精密歯車加工といえば、 Runsom精密 お手伝いする準備ができています。当社は、さまざまな材料を使用したカスタムの精密ギアの製造を専門としています。 CNC加工サービス。当社の驚異的な製造能力により、ギアや機械部品の製造はより速く、より合理化され、著しく効率的になります。今すぐ当社の専門家にご連絡ください。 瞬時に引用 そして次のプロジェクトを始めましょう。
当社について詳しく見る カスタムギアの製造 能力。
興味があるかもしれないその他の記事: