機械加工または仕上げ表面の品質に関しては、常に「表面粗さ」と「表面仕上げ」という 2 つの関連用語が存在します。これらはしばしば同じ意味で使用されますが、科学的には同じではなく、明確な違いがあります。
表面粗さは表面の不規則性の定量化可能な測定値を指しますが、表面仕上げは外観に基づく、または粗さ値から間接的に定性的に評価されます。 ただし、 機械工場表面仕上げという用語は、表面粗さのみを表すために使用されるのが一般的です。
この記事では、表面粗さと表面仕上げの属性、値、測定、特徴の違いに焦点を当てます。さらに、参考として、いくつかの一般的な製造プロセスで得られる代表的な粗さの表と、一般的な表面粗さの換算表も提供します。さらに詳しく見ていきましょう。
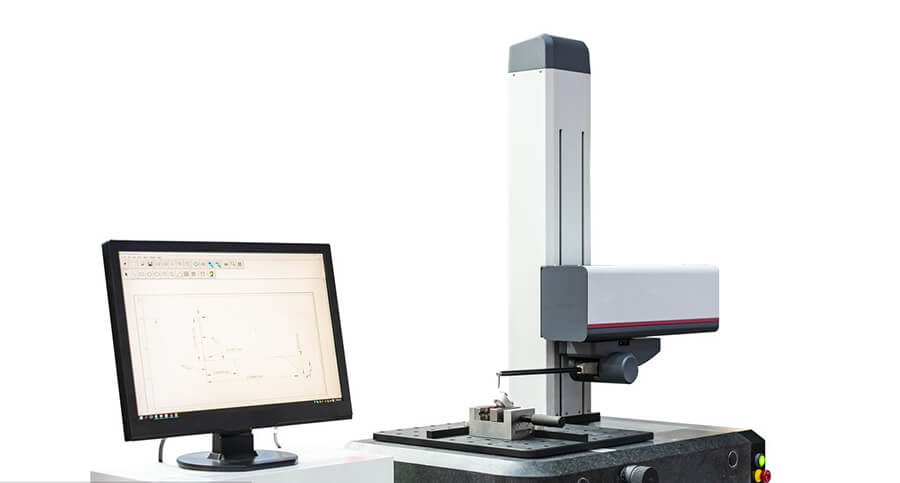
表面粗さとは何ですか?
粗さとしても知られる表面粗さは、一般的に指定、測定、計算される表面仕上げの重要な側面です。これは、理想的な形状と比較した実際の表面の法線ベクトルの方向の変化によって定義されます。これらの変動が大きい場合、表面は粗いとみなされ、変動が最小限の場合、表面は滑らかであると考えられます。
表面計測では、粗さは通常、測定表面の高周波成分と短波長成分に関連付けられます。ただし、実際のアプリケーションでは、表面が意図した目的に適しているかどうかを判断するために、振幅 (偏差の大きさ) と周波数 (偏差が発生する頻度) の両方を考慮する必要があることがよくあります。
表面仕上げとは何ですか?
表面仕上げ は表面のテクスチャを指し、多くの場合、表面テクスチャという用語と同じ意味で使用されます。これは、粗さ、レイ、うねりの 3 つの主要な要素で構成されます。製造された製品の表面仕上げは、製造時に使用される材料とプロセスに基づいて大きく異なる場合があります。
表面仕上げの仕様は一般的に次の表に示されています。 技術的な図面 為に 機械部品特に、パーツをしっかりと嵌め合わせたり、相互に作用させたり、シールを作成したりする必要がある場合に最適です。技術図面の表面指示記号を適切に指定して解釈するには、 ASME (米国機械学会) は、1,436 万円の表面テクスチャ シンボル標準を発行しました。 ASME は、表面仕上げの定義と測定方法を提供する B41.6 表面質感規格も発行しています。
最終製品が望ましい性能基準を確実に満たすためには、表面要件を明確かつ効果的に伝達することが不可欠です。表面仕上げ要件を含めない、正確に指定しない、または適切に解釈しないと、最終製品の性能とコストに重大な影響を与える可能性があります。
さまざまな表面仕上げ
一般に、製品に高い純度が要求される場合、製造装置にはより微細な表面仕上げが必要になります。たとえば、 2B仕上げ は、ベーキング装置、食品加工、製薬装置、真空ドラム乾燥機、タンクや容器で一般的に使用されています。この仕上げは滑らかであると考えられており、場合によっては研磨された #4 仕上げよりも滑らかであると考えられており、どちらも会議で許容されます。 USDA規格。 2B 仕上げの平均粗さ (Ra 値) は、金属のゲージに応じて、通常 0.3 (12) ~ 1μ (40) の範囲です。
比較のため、他の仕上げとそれに対応する粗さの平均をいくつか示します。
- #1 仕上げは、熱間圧延、焼鈍、酸洗 (HRAP) とも呼ばれ、工場から出たときのプレート材料の初期状態です。表面は非常に粗く、通常 3.2 (125) ~ 12.5 (500) Ra の範囲であり、研磨剤の塗布などの機械的仕上げプロセスは一切受けていません。
- #4 仕上げは、#3 および #6 仕上げとともに「ブラッシュド」仕上げと呼ばれることが多い柾目仕上げです。標準的な #4 仕上げの Ra 値は通常約 0.8 (32) ですが、#4 乳製品または衛生仕上げの平均粗さは 0.3 (12) Ra ~ 0.4 (16) Ra です。
- 他の 2 つの仕上げ、#7 と #8 はバフ仕上げです。 #8 仕上げの表面はほぼ完璧で、Ra 値は 0.025 (1) Ra と非常に低くなります。
他にも多くの仕上げが利用可能ですが、注射剤や耳用溶液などのバイオ医薬品用途では、通常、電解研磨による約 0.38 (15) Ra の表面仕上げが指定されており、BPE SF-4 規格に準拠しています。粉末および錠剤のメーカーは、電解研磨を必要としないため、BPE SF-2 規格に基づく約 0.5 (20) Ra のわずかに粗い表面仕上げを利用できる場合があります。
表面粗さと表面仕上げの違い
表面仕上げは、粗さ、レイ、うねりの 3 つの主要な要素で構成されます。これらの中で、最も一般的に指定される表面仕上げの側面は粗さです。
粗さは、機械加工後の仕上げ表面に存在するマクロおよびミクロの両方の凹凸および不規則性の測定を指します。これは、これらの表面凹凸の山の高さと谷の深さを定量的に示します。粗さを測定するには、正確な測定を容易にするさまざまな機器が利用可能です。

対照的に、表面仕上げは、表面の全体的な外観と品質を定性的に説明および指定します。これは、表面を視覚的に観察するか、粗さの値を考慮することによって行うことができます。悪い、悪い、良い、光沢がある、細かいなどの記述的属性は、仕上げ品質を特徴付けるために使用されます。表面仕上げは粗さと異なり数値化できず、人間の主観に左右されます。
この表は、表面粗さと表面仕上げの主な違いをまとめたものです。
表面粗さ | 表面仕上げ |
表面凹凸の定量測定 | 表面品質の定性評価 |
山の高さと谷の深さを数値で提供します | 悪い、悪い、良い、光沢がある、細かいなどの属性によって記述されます。 |
特定の機器を使用して測定 | 視覚的に、または粗さの値に基づいて決定されます |
客観的な測定 | 主観的な評価 |
摩擦や摩耗などの機能面の評価に役立ちます | 表面の全体的な外観と美的魅力を示します。 |
定量的および定性的価値
すべての物理パラメータを測定でき、その値は数値と対応する単位を使用して表されます。定量的測定では、常に単位とともに数値が提供されます。表面粗さは測定可能なパラメータの例です。たとえば、マイクロミリングされた表面の平均粗さは 325 ナノメートルです。一方、仕上がりは数値では表現できない定性的なパラメータです。代わりに、仕上がりを説明するために、良い、悪い、悪い、粗いなどの属性が使用されます。
主観的パラメータと人間の知覚
表面仕上げの属性は主観的なものであり、特定の用途や望ましい結果に依存します。たとえば、ケーシングとしては良好な仕上げであると考えられるフライス加工された表面は、それが用途に使用される場合には、仕上げが悪いと見なされる可能性があります。 ボールベアリング。ただし、粗さは用途に関係なく同じままです。アプリケーションから独立しており、人間の偏見の影響を受けません。人間にはさまざまな好みがあるため、ある人が良いと思う仕上がりでも、別の人はそうではないこともあります。したがって、表面仕上げの説明に使用される属性は、科学的な文脈では適用範囲が限られています。
測定器
表面粗さは、接触式、非接触式を問わず、市場で簡単に入手できるさまざまな測定器を使用して正確に測定できます。これらの機器にはさまざまな機能が備わっています。使用する特定の測定器に関係なく、粗さは基本的に、物体の表面の山の高さと谷の深さの測定値です。一方、表面仕上げは機器を使用して直接測定することはできません。代わりに、表面粗さの値が表面の仕上げを指定する間接的な指標として使用されます。
他のパラメータによる評価
さまざまな製造プロセスにより、さまざまなレベルの表面仕上げが生成されます。通常、機械加工などのプロセスには、サーフェス生成や、次のような表面修正技術が含まれます。 熱処理, コーティング、および着色により、粗さが低下する傾向があります。ただし、粉末冶金や インベストメント鋳造 高品質な表面も提供できます。粗さの推定は、さまざまなプロセスパラメータとプロセスで使用される関連機器の機能を考慮することで実行できます。たとえば、鋭利な工具を使用した加工では、推定粗さは次のようなパラメータを使用して表現できます。 送り速度、主切れ刃角度と補助切れ刃角度。ただし、表面仕上げを同じ方法で評価することはできません。
表面粗さの比較表 – 加工プロセスごとの Ra 値
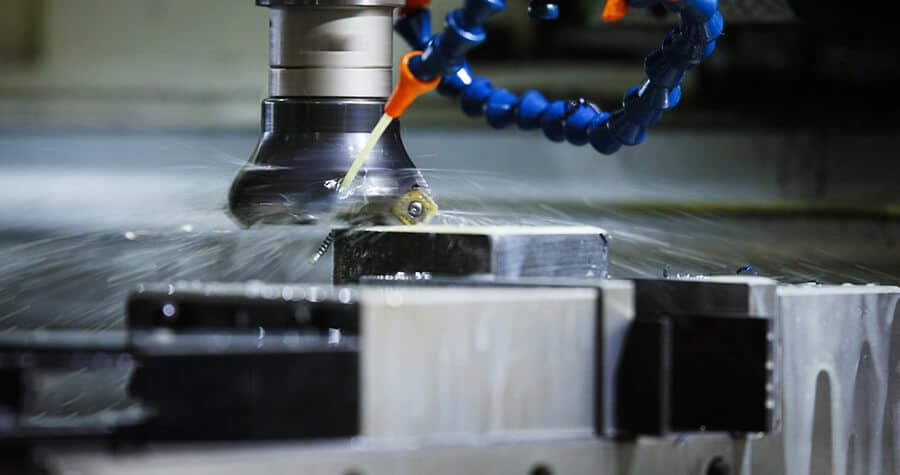
部品の表面仕上げの品質は、使用される製造プロセスに大きく影響され、非常に滑らかな仕上げを達成するには、多くの場合、研削や研磨などの追加の手順が必要になります。粗さの仕様が主要な製造プロセスの制限内に収まることを確認することが重要です。
一部の製造プロセスでは、装置の機能内で表面仕上げをある程度制御できます。たとえば、フライス加工または旋削加工では、浅い切り込み深さと遅い送り速度を使用すると、通常、より滑らかな仕上げが得られますが、より深い切り込みとより速い速度では、より粗い仕上げが得られます。切削工具の状態も表面仕上げに影響を与える可能性があります。
下の図は、一般的な製造プロセスの相対的な表面粗さを示しています。
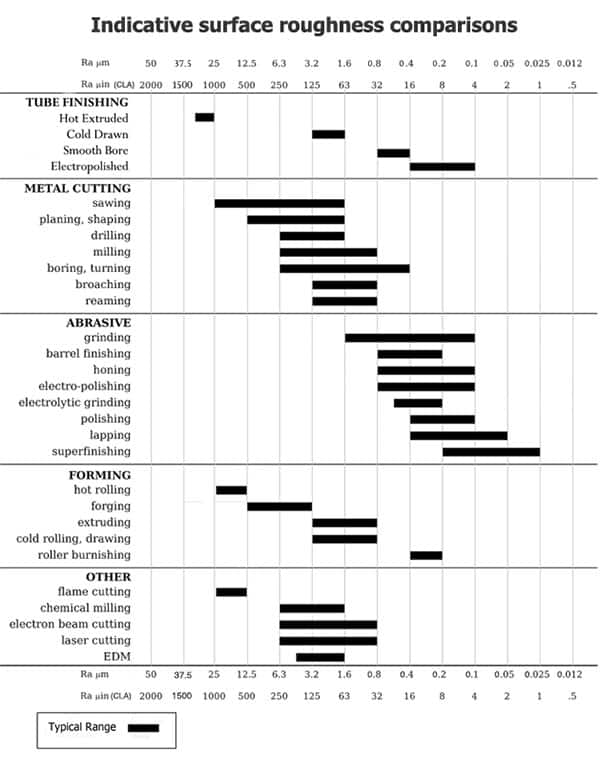
表面粗さ換算表
一般的な表面粗さの換算表は次のとおりです。
グリットNo. | 粗さ、N | 粗さ値、Ra | RMS (μインチ) | 中心線の平均、CLA | 粗さ、室温 | |
ISO番号 | マイクロメートル (μm) | マイクロインチ (μインチ) | (μインチ) | (μm) | ||
---- | N12 | 50 | 2000 | 2200 | 2000 | 200 |
---- | N11 | 25 | 1000 | 1100 | 1000 | 100 |
---- | N10 | 12.5 | 500 | 550 | 500 | 50 |
60 | N9 | 6.30 | 250 | 275 | 250 | 25 |
---- | N8 | 125 | 137.5 | 125 | 13 | |
80 | ---- | 1.80 | 71 | 78 | 71 | 9.0 |
---- | N7 | 1.60 | 63 | 64.3 | 63 | 8.0 |
120 | ---- | 1.32 | 52 | 58 | 52 | 6.6 |
150 | ---- | 1.06 | 42 | 46 | 42 | 5.3 |
---- | N6 | 0.80 | 32 | 32.5 | 32 | 4.0 |
180 | ---- | 0.76 | 30 | 33 | 30 | 3.8 |
220 | ---- | 0.48 | 19 | 21 | 19 | 2.4 |
---- | N5 | 0.40 | 16 | 17.6 | 15 | 2.0 |
240 | ---- | 0.38 | 15 | 17 | 12 | 1.9 |
320 | ---- | 0.30 | 12 | 14 | 9 | 1.5 |
400 | ---- | 0.23 | 9 | 10 | 8 | 1.3 |
---- | N4 | 0.20 | 8 | 8.8 | 4 | 1.2 |
500 | N3 | 0.10 | 4 | 4.4 | 2 | 0.8 |
---- | N2 | 0.05 | 2 | 2.2 | 1 | 0.5 |
---- | N1 | 0.025 | 1 | 1.1 | 1 | 0.3 |
表面粗さの記号: Ra vs Rz
Ra と Rz はどちらも表面粗さを定量化するために使用される測定値ですが、具体的な意味と計算方法が異なります。
Ra (平均表面粗さ) は、表面の山と谷の間の平均距離、および指定されたサンプリング長さ内の平均線からの偏差を表します。測定領域全体の粗さの平均値が得られます。
一方、Rz、つまりプロファイルの最大高さの平均は、5 つのサンプリング長のセット内の最高の山と最低の谷の間の最大の差を測定します。これは、表面上の高さの最大変化を示します。
Ra は平均的な測定値を提供しますが、テストされた部品の特定の表面の特徴を完全には捉えていない可能性があります。場合によっては、異なる方法で処理された表面が同じ Ra 値を持つことがあります。この制限に対処するために、誤差を排除し、表面粗さのより包括的な評価を提供するために Rz が使用されることがあります。
機械加工におけるさまざまな材料の Ra 値
さまざまな材料の表面仕上げ要件 CNC加工 加工プロセスなどの要因によって異なりますが、 切削速度、工具形状、切込み深さなど。一般的な金属の典型的な範囲をいくつか示します。
- スチール: スチールの Ra 値は、特定の加工プロセスに応じて 0.2 μm から 3 μm まで変化します。たとえば、旋削加工では通常 0.4 μm ~ 1 μm の Ra 値が得られますが、研削加工ではさらに低い約 0.2 μm の Ra 値を達成できます。
- アルミニウム: アルミニウムは一般に鋼に比べて Ra 値が低く、0.1 μm ~ 1 μm の範囲です。通常、旋削およびフライス加工のプロセスでは Ra 値が 0.2 μm ~ 0.5 μm になりますが、研削では 0.1 μm という低い Ra 値を達成できます。
- 銅: 銅の Ra 値は 0.1 μm ~ 1 μm の範囲内にあります。旋削およびフライス加工プロセスでは通常、0.2 μm ~ 0.5 μm の Ra 値が得られますが、研削加工では 0.1 μm という低い Ra 値を達成できます。
- チタン: チタンは鋼に比べて Ra 値が高く、0.5 μm ~ 4 μm の範囲を持つ傾向があります。旋削およびフライス加工プロセスでは一般に 0.8 μm ~ 1.5 μm の Ra 値が得られますが、研削加工では 0.5 μm という低い Ra 値を達成できます。

Rz 値をいつ使用するか?
Rz 値は、次の状況で使用する必要があります。
- 非常に粗いまたは滑らかな表面の場合は、作業およびテスト条件を考慮して、表面粗さをより正確に評価するために Rz を使用することをお勧めします。
- 柔らかい材料を扱う場合は、Ra の代わりに Rz を使用する必要があります。これは、針をなぞる Ra 測定では柔らかい材料の表面に傷がつき、不正確な結果が生じる可能性があるためです。
- 測定領域が非常に小さく、サンプリング長さ内の内部輪郭の山または谷が 5 つ未満である場合は、表面粗さの測定に Rz を使用する必要があります。
- ある部品を扱うときは、 疲労強度 要件に応じて、Rz は表面仕上げを評価するために考慮する適切なパラメータです。
表面粗さの測定方法?
表面粗さは、表面が望ましい形状からどれだけ逸脱しているかを指します。通常、さまざまな方法を使用して測定されます。
連絡方法: 表面と物理的に接触して粗さを測定するプローブの使用が含まれます。最も一般的な接触方法はスタイラス法です。この方法では、スタイラスを表面上で移動させ、たわみを測定して記録します。

非接触方式: 物理的接触なしで表面粗さを測定するために使用されます。これらの方法では通常、レーザーや光学システムなどの技術を使用して表面をスキャンし、反射光または散乱光に基づいて粗さを決定します。光学的方法は、光を表面に投影し、その反射光を測定して粗さを評価する一般的な非接触アプローチです。

画像解析: カメラまたは顕微鏡を使用して表面の画像をキャプチャし、それらを分析して表面粗さを測定します。この方法は、他の方法では効果的に測定できない複雑な詳細や微細な特徴を持つ表面に特に役立ちます。
インプロセスメソッド: 機械加工またはその他のプロセス中に表面をリアルタイムで監視できるため、オペレータは貴重なフィードバックを受け取ることができます。これらの方法は、実際の用途によく似た条件下で表面を測定するため、他の技術と比較してより正確な結果が得られる可能性があります。
比較テクニック: 評価対象の表面と同じ装置、プロセス、材料を使用して作成された表面粗さサンプルを使用します。これらのサンプルは、表面粗さの既知の標準と視覚的および触覚的に比較されます。これらの方法は、プロセスが主観的な判断に依存するため、重要ではないアプリケーションでよく使用されます。
製造における表面粗さの重要性
まず、表面粗さは表面テクスチャの重要な要素であり、オブジェクトがその環境とどのように相互作用するかに大きな影響を与えます。表面に凹凸があると亀裂や腐食が発生する箇所が生じ、機械部品の性能や耐久性に影響を与える可能性があります。
トライボロジーの分野では、粗い表面は摩耗が多くなり、摩耗が大きくなる傾向があります。 摩擦係数 滑らかな表面と比較して。これは、メーカーがさまざまな用途に適した材料と表面仕上げを選択し、製品の性能と寿命を最適化するのに役立ちます。
さらに、表面粗さを意図的に操作して、特定の結果を達成することもできます。例えば塗装などの密着性が求められる用途では、 パウダーコーティング、またはメッキの場合、ある程度の粗さはコーティングの密着性を高めるのに役立ちます。
メーカーやエンジニアにとって、表面粗さの制御を維持することは非常に重要です。これには、表面粗さを監視および測定して、指定された制限内に収まっていることを確認することが含まれます。これにより、メーカーは一貫した信頼性の高い生産プロセスを実現し、顧客の要件を満たす高品質の製品を生み出すことができます。
よくある質問
結論
望ましい表面品質は、機械加工部品の重要な側面です。表面仕上げは、製造部品の表面粗さを望ましいレベルに達成するために実行される特定の手順です。これは、使用される製造プロセスの影響を受け、最終製品の機能、外観、寿命に影響を与える重要な要素です。
表面仕上げを指定するパラメータの中で、最も具体的に考慮されるのは粗さです。粗さの値が高いと、摩擦が増大し、部品の早期故障が発生する可能性があります。したがって、表面仕上げと表面粗さ、およびそれらの変化を包括的に理解することが重要です。
カスタム品質の表面仕上げソリューションプロバイダー – Runsom Precision

製造プロセスに関しては、部品の構成、強度、寸法、公差などの要素を優先する傾向があります。ただし、表面粗さも考慮すべき重要な要素です。表面が粗すぎると、摩擦が増加し、部品が早期に故障する可能性があります。
正確な表面粗さを実現することは困難であり、コストがかかる場合があります。ここで専門の仕上げチームが役立ちます。で Runsom精密、カスタム精度が必要かどうかにかかわらず、お客様のニーズを満たすワンストップの加工ソリューションを提供します。 CNC加工サービス または高品質の表面仕上げ。当社の専門知識は、プラスチック、ゴム、シリコン、セラミック部品だけでなく、アルミニウム、チタン、ステンレス鋼、真鍮、銅などのさまざまな材料にも及びます。
プロジェクトの要件について話し合い、製品に最適な機械加工プロセスと表面仕上げを決定するには、 瞬時に引用 また 弊社の専門家にお問い合わせください。私たちは、お客様のプロジェクトで最適な結果を達成できるようお手伝いいたします。
興味があるかもしれないその他の記事: