Engranajes han persistido durante siglos, lo que los convierte en uno de los elementos mecánicos más antiguos pero aún pertinentes en la actualidad.
Varios métodos, incluyendo fundiciónPara fabricar engranajes se pueden emplear forja, extrusión, pulvimetalurgia, corte y fresado de engranajes. No existe un proceso único para la fabricación de engranajes, ya que requieren diferentes procesos según el tipo y la aplicación. Sin embargo, el proceso de mecanizado tiene una importancia significativa para lograr el tamaño, la forma y la calidad del engranaje. acabado de la superficie.
Esta guía explorará la fabricación de engranajes y cubrirá procesos comunes, operaciones de posprocesamiento y materiales.

¿Qué es la fabricación de engranajes?
El proceso de fabricación de engranajes implica la producción y conformación precisa de los engranajes, que son componentes esenciales utilizados en la maquinaria para transmitir. esfuerzo de torsión. Los engranajes, conocidos por su movimiento de rotación, tienen dientes que se entrelazan con los de otro mecanismo dentado, lo que permite una transferencia suave de potencia mecánica.
La creación de engranajes se realiza mediante varios métodos, incluido el mecanizado, la pulvimetalurgia, la fundición y el estampado. El fresado, el brochado y el cojeo de engranajes se encuentran entre las técnicas más precisas y populares utilizadas para lograr perfiles de engranajes intrincados y bien definidos. Estos métodos garantizan la elaboración precisa de los engranajes necesarios para diversas aplicaciones en maquinaria.
En la construcción de engranajes se utilizan diversos materiales, como metales, plásticos e incluso madera. El progreso tecnológico ha permitido la formación de engranajes metálicos y plásticos mediante fundición a presión o moldeo por inyección, ofreciendo métodos de fabricación alternativos. Esto permite a los fabricantes explorar opciones más allá de la producción tradicional de engranajes. Sin embargo, es esencial reconocer que algunas situaciones requieren operaciones de posprocesamiento para mejorar la calidad del producto final.

Procesos típicos de fabricación de engranajes
Los métodos de fabricación de engranajes se han clasificado típicamente en tres categorías principales: generación, conformación y corte de forma.
- La conformación de engranajes crea engranajes sin utilizar herramientas de corte (es decir, fundición, forja, pulvimetalurgia, impresión 3D).
- El corte de formas de engranajes implica herramientas que se utilizan para crear el perfil del engranaje (es decir, fresado de engranajes, brochado y electroerosión).
- La generación de engranajes utiliza herramientas de corte con la forma del perfil de engranaje deseado para crear el engranaje (es decir, modelado de engranajes y tallado de engranajes).
Formación de engranajes
Fundición
La fundición es un proceso de modelado en el que se vierte metal fundido en la cavidad de un molde para crear formas. Es un proceso relativamente sencillo que se utiliza principalmente para producir piezas en bruto o cilindros para engranajes, mientras que los dientes generalmente se elaboran mediante mecanizado.
Sin embargo, hay un área específica donde la fundición reina como método de fabricación preferido en la industria: la producción de engranajes de gran tamaño. Los métodos de mecanizado y otras técnicas de formación de engranajes son menos prácticos para diámetros grandes. Por lo general, los engranajes más grandes son predominantemente del tipo de engranaje recto, lo que hace que la fundición sea una excelente opción debido a su relativa simplicidad.
Fundición de conchas, fundición a presión, moldeo en arena, y fundición en molde permanente son los tipos más frecuentes de métodos de fundición utilizados para la producción de engranajes.

Forjar
Este proceso ofrece la flexibilidad de producir tanto espacios en blanco como engranajes terminados según requisitos específicos. La forja es especialmente adecuada para engranajes relativamente sencillos.
En teoría, la forja es un excelente método de fabricación de engranajes para aplicaciones de servicio pesado debido a un razonamiento simple. El tratamiento térmico involucrado en la forja da como resultado engranajes con propiedades de fatiga mejoradas. Sin embargo, la fuerza sustancial requerida para la forja restringe el tamaño y la delgadez de los engranajes producidos.
Normalmente, el forjado es eficaz para engranajes de entre 6 y 10 pies de diámetro. Dependiendo del tipo de forjado, como el forjado de precisión, el mecanizado puede ser necesario o no para el producto final del engranaje.

Fabricación aditiva
Fabricación Aditiva, comúnmente conocida como Impresión 3d, opera construyendo un objeto tridimensional capa por capa, basado en un modelo CAD 3D. Este enfoque permite que las máquinas aditivas produzcan diseños complejos, incorporando estructuras reticulares diseñadas para reducir la masa, una hazaña que no se puede lograr fácilmente con métodos tradicionales. La creación de tales geometrías a menudo implica el uso de topología 3D optimización y diseño computacional generativo.
Se pueden utilizar procesos de fabricación aditiva para fabricar engranajes convencionales y no circulares. Además, las impresoras 3D de alta calidad ahora tienen un precio razonable y son fácilmente accesibles.
Metalurgia de polvos
Metalurgia de polvos Sirve como un método de conformado de alta precisión que presenta una alternativa rentable a los engranajes tradicionales de acero y hierro fundido con acabado mecanizado. Sin embargo, no es adecuado para tamaños de engranajes más grandes y, en cambio, destaca por producir piezas pequeñas y de alta calidad. estimular, bisely engranajes en espiral.
La porosidad del material resultante en engranajes más grandes conduce a una reducción de la fatiga y la resistencia al impacto, limitando su capacidad de carga. No obstante, emplear un proceso de sinterización puede mejorar sus propiedades mecánicas.
Este método resulta ventajoso para diseños de engranajes que incorporan características como agujeros, depresiones y niveles o proyecciones de superficie variables. A pesar de estos beneficios, el costo inicial de instalación de la pulvimetalurgia es considerablemente alto, lo que la hace poco práctica para la producción de bajo volumen.

Borrado
El corte, similar a la extrusión, comparte muchas similitudes pero tiene limitaciones en sus capacidades tridimensionales. Este método de formación de engranajes emplea láminas de metal y múltiples troqueles para lograr la forma deseada. Se pueden producir varios tipos de engranajes mediante el proceso de corte, y los engranajes rectos ofrecen resultados óptimos.
En la actualidad, el proceso de corte encuentra aplicación en la producción de engranajes en múltiples industrias, particularmente para usos livianos. Estos incluyen equipos de oficina, sistemas hidráulicos, pequeños dispositivos médicos y otras aplicaciones con demandas de carga relativamente bajas.
Corte de forma de engranaje
Molienda
El fresado de engranajes implica el uso de una herramienta de corte de forma en un fresadora para tallar dientes de engranajes a partir de un material en bruto. Este proceso de mecanizado fundamental se basa en el movimiento entre una cortadora giratoria de múltiples filos y una pieza de trabajo para dar forma a los dientes de engranajes individuales.
Si bien el método de corte por fresado tiene una aplicación algo restringida, sobresale en la producción de geometrías de engranajes intrincadas y puede ejecutar cortes personalizados sin requerir herramientas especiales.
El fresado CNC se emplea comúnmente para fabricar ruedas dentadas helicoidales y rectas para diversas industrias, como transmisiones de automóviles, así como cortadoras de fresado.

Brochado
El brochado se destaca como una de las técnicas más rápidas para cortar formas de engranajes. Emplea una herramienta de corte de varios dientes conocida como brocha, y cada diente suele ser más alto que el anterior. Esta variación incremental de altura facilita la creación de cortes más pequeños y fáciles, lo que produce rápidamente la forma deseada sin sacrificar la precisión.
Si bien este método de producción de engranajes se asocia comúnmente con engranajes internos, también se presta para crear dientes externos. Para lograr esto, se ha creado una herramienta especializada para “brochado de ollas”, lo que garantiza la replicación del mismo nivel de precisión y eficiencia.
Mecanizado por descarga eléctrica (EDM)
La electroerosión representa una técnica de fabricación electromecánica en la que se elimina material de una pieza de trabajo provocando una secuencia de descargas de corriente entre dos electrodos divididos por un baño dieléctrico líquido. En lugar de cortar, la chispa sirve como una “herramienta de corte” que esencialmente erosiona el material.
La electroerosión sobresale en el corte de geometrías intrincadas de todos los tamaños, incluso como proceso de corte de engranajes. Sin embargo, el método tiene sus inconvenientes. La ausencia de un control y una programación precisos puede provocar daños en las superficies de las piezas, lo que supone un desafío particular para los programas CNC que ejecutan perfiles de dientes curvos. Sin embargo, la aplicación de alta calidad y fácil de usar modelado 3D y el software CAM, como Feature CAM, Autodesk Fusion, Master CAM y otros, pueden facilitar el movimiento suave necesario para cortar dientes curvos.
En los últimos años, las máquinas de electroerosión han experimentado mejoras, disminuyendo los problemas con los acabados superficiales y elevando la precisión del corte y las propiedades de los materiales resultantes (microestructura, propiedades mecánicas, etc.). Este proceso puede lograr tolerancias estrictas de tan solo milésimas de pulgada y crear engranajes tanto diminutos (con una fracción de pulgada de diámetro) como grandes (con un diámetro superior a 20 pulgadas). La electroerosión se emplea para aplicaciones delicadas en relojes, así como para cortar engranajes robustos, incluidos los utilizados en coches de carreras.

Generación de engranajes
Tallado de engranajes
El proceso de tallado de engranajes implica el uso de un dispositivo de corte cónico conocido como fresa, en el que tanto la fresa como la pieza de trabajo giran mientras la fresa gira alrededor del engranaje en bruto.
Principalmente, los engranajes rectos se producen utilizando este método, aunque una variedad de otros engranajes, incluidos los cicloides, engranajes helicoidales, engranajes helicoidales, trinquetes y piñones, todos se fabrican mediante tallado. La calidad de la encimera es de suma importancia, especialmente al cortar geometrías complejas.
El tallado de engranajes generalmente no es adecuado para engranajes internos. De manera similar a la conformación de engranajes, el tallado con fresado ofrece ventajas de configuración, pero se limita a cortes externos, ya que la fresa talla el exterior de los engranajes en bruto.

Conformación de engranajes
El proceso de conformación del engranaje implica una fresa con un perfil que coincide con la geometría del diente deseada. Esta herramienta de corte utiliza un movimiento lineal para eliminar material del engranaje en bruto, que comprende una carrera de corte y retorno. El paso de la herramienta de conformación de engranajes se alinea con el paso requerido para el diente del engranaje, acomodando engranajes con diferentes cantidades de dientes.
La conformación de engranajes demuestra ser una solución viable para tiradas de producción de tamaño mediano, ya que ofrece ventajas de velocidad, diseño y configuración para la producción en masa y facilita la creación de la mayoría de los tipos de engranajes, con la excepción de los engranajes helicoidales y los engranajes internos. Sin embargo, el inconveniente de la configuración del engranaje radica en la rigidez limitada del brazo de corte, lo que da como resultado una precisión reducida.
Método Sunderland
Entre las principales técnicas de fabricación de engranajes, las cortadoras de cremallera desempeñan un papel destacado. El proceso de corte de cremalleras, también conocido como Método Sunderland o Sistema Sunderland, implica una máquina de engranajes equipada con una cortadora de cremalleras con ángulos de inclinación y de separación para dar forma a los perfiles de los dientes en un engranaje en bruto. Este método se basa en el movimiento relativo específico entre la pieza de trabajo y la cortadora durante el mecanizado, similar a un piñón y cremallera.
El método Sunderland destaca por producir formas de dientes uniformes y, en teoría, los engranajes cortados con el mismo cortador son capaces de engranar correctamente entre sí. Como resultado, mediante este método se pueden producir eficazmente diseños de engranajes que requieren alta precisión, incluidos engranajes de doble hélice. Además, el método Sunderland demuestra ser versátil y rentable, especialmente para tiradas de producción de volumen medio a alto.
Postprocesamiento para la fabricación de engranajes
Una vez finalizados los procesos de fabricación de engranajes detallados anteriormente, es posible que el acabado de la superficie y la precisión dimensional de los engranajes no cumplan con los requisitos específicos para ciertas aplicaciones. En consecuencia, se hace necesaria una serie de operaciones de acabado. Estas actividades de posprocesamiento abarcan una variedad de tratamientos, incluido el tratamiento térmico para mejorar las características de fatiga, así como la corrección dimensional y el acabado de superficies.
A continuación se detallan los cinco procesos de acabado de superficies más comunes que se emplean con frecuencia en la producción de engranajes.
- Pulido: este conocido proceso de acabado de superficies proporciona eficazmente un acabado suave en toda la superficie, como su nombre lo indica. Se puede ejecutar de forma intermitente o continua sin afectar los resultados.
- Lapeado: Adecuado para engranajes delicados que requieren máxima precisión, el lapeado emplea pequeñas partículas abrasivas para alisar meticulosamente una superficie a velocidades bajas o medias.
- Bruñido: Otro proceso muy utilizado, el bruñido pule la superficie, impartiendo una textura suave y al mismo tiempo corrigiendo errores menores en la geometría del diente.
- Afeitado: Implica la eliminación de capas extremadamente delgadas de la superficie para lograr un perfil suave. El afeitado es un proceso relativamente costoso y rara vez se utiliza en la producción de engranajes.
- Bruñido: esta técnica implica utilizar compresión para refinar la superficie, esencialmente alisándola.
Materiales disponibles para la fabricación de engranajes
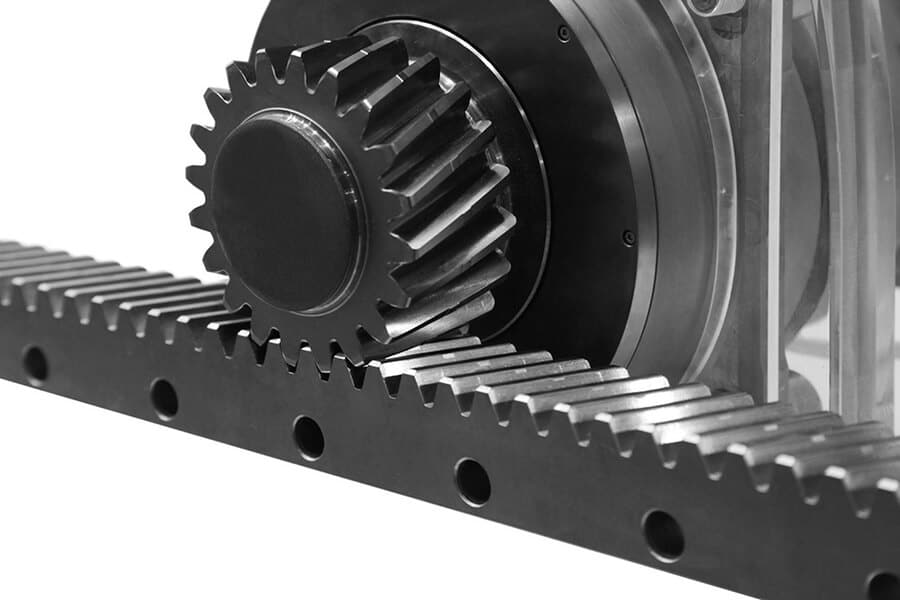
Para un rendimiento confiable y una vida útil prolongada, un engranaje debe poseer características específicas, que incluyen:
- Bajo coeficiente de fricción
- Excelente capacidad de fabricación
- Alta resistencia a la tracción para soportar cargas estáticas.
- Alta resistencia para soportar variaciones de carga.
Se emplean numerosos materiales en la producción de engranajes para impartir estas propiedades críticas. A continuación se muestra un resumen de cada material y sus puntos fuertes distintivos.
Hierro fundido
El hierro fundido puede soportar un desgaste repetido y sostenido, lo que lo hace muy adecuado para la fabricación de engranajes de precisión. El proceso de fundición permite la producción de formas complejas de engranajes con facilidad. Los engranajes de hierro fundido se utilizan con frecuencia en aplicaciones donde la acción suave no es una preocupación principal.
Acero
Los engranajes fabricados con aleaciones de acero presentan una alta resistencia, ya que comúnmente están sujetos a tratamiento térmico para mejorar la tenacidad y dureza, especialmente en los dientes. Notablemente, acero carbono se utiliza en la producción de cremalleras helicoidales, rectas, cónicas, helicoidales y de engranajes.
Latón
El latón, una combinación de cobre y zinc, es una aleación que permite a los fabricantes ajustar el contenido de zinc. El latón con bajos niveles de zinc ofrece una mayor ductilidad en comparación con otros materiales, y su base de cobre hace que el metal sea antimicrobiano y fácil de mecanizar. Normalmente, los engranajes de latón se emplean en aplicaciones de baja carga, como engranajes rectos o cremalleras.
Bronce
Además del latón, otras aleaciones de cobre también contienen bronce de aluminio y aleaciones de bronce fosforado. Estos engranajes no magnéticos son los más adecuados para su uso en ambientes corrosivos.
Combinando cobre, estaño y fósforo, el bronce fosforoso ofrece mayor resistencia y resistencia a la corrosión debido a la presencia de estaño, mientras que la adición de fósforo mejora su rigidez y resistencia al desgaste. Esto hace que los engranajes de bronce fosforado sean muy adecuados para entornos de alta fricción, particularmente en engranajes helicoidales, ya que el material resiste eficazmente la fricción causada por la rueda y minimiza los efectos de la lubricación.
Compuesto de cobre, aluminio, níquel, hierro y manganeso, el bronce de aluminio exhibe una resistencia excepcional contra el desgaste y la corrosión, lo que lo convierte en la opción preferida para su uso en entornos altamente corrosivos expuestos al agua salada, la oxidación y Ácidos orgánicos. Además, su capacidad para prosperar en entornos de alta carga lo hace adecuado para aplicaciones que involucran ruedas helicoidales y engranajes helicoidales.
Aleaciones de Aluminio
En entornos que exigen engranajes con una alta relación resistencia-peso, las aleaciones de aluminio sirven como un sustituto viable de las aleaciones de hierro. Además, los engranajes fabricados con aleaciones de aluminio se benefician de un acabado superficial protector llamado pasivación, que los protege contra la corrosión y la oxidación.
Las aleaciones de aluminio predominantes utilizadas en la fabricación de engranajes comprenden 2024, 6061, y 7075. Independientemente del grado, los engranajes de aluminio son los más adecuados para aplicaciones con temperaturas bajas a moderadas, ya que comienzan a degradarse aproximadamente a 400 °F.
Metales en polvo
Estos metales constan de varias combinaciones de materiales metálicos, incluido acero de hierro y níquel, acero prealeado y mezclas personalizadas. Además, su porosidad contribuye a un funcionamiento más silencioso de los engranajes y pueden volverse autolubricantes mediante impregnación al vacío con diferentes aceites.
El proceso implica tres pasos clave:
- Desarrollar la combinación óptima que se alinee con las especificaciones de durabilidad, precisión y confiabilidad.
- Compactar la mezcla bajo presión controlada para cumplir con los requisitos exactos.
- Calentar o sinterizar la mezcla para obtener una forma permanente.
La pulvimetalurgia es capaz de producir engranajes cónicos, cónicos en espiral, rectos, helicoidales, de piñón y combinados.
Termoplásticos
En la fabricación de precisión, los engranajes ligeros dependen en gran medida de termoplásticos. Estos engranajes se pueden producir de manera similar a los engranajes metálicos, con moldeo por inyección siendo a menudo el método preferido. El acetal es una opción popular entre los fabricantes debido a su estabilidad en amplios rangos de temperatura, baja coeficiente de friccióny resistencia a la fluencia.
Proveedor de soluciones de fabricación de engranajes personalizados: Runsom Precision
Operar dentro del campo altamente especializado de la fabricación de engranajes exige alta precisión y exactitud. Debido a su papel crucial en los sistemas mecánicos, incluso las imperfecciones de fabricación más pequeñas pueden tener consecuencias graves. Por ello, se recomienda elegir cuidadosamente su proveedor de servicios.
Cuando se trata de mecanizado de engranajes de precisión, Precisión Runsom está listo para ayudar. Nos especializamos en la fabricación de engranajes de precisión personalizados utilizando una variedad de materiales a través de nuestra Servicios de mecanizado CNC. Con nuestras increíbles capacidades de fabricación, la fabricación de engranajes y piezas mecánicas se vuelve más rápida, más ágil y notablemente más eficiente. Comuníquese con nuestros expertos hoy para una cotización instantánea y comienza tu próximo proyecto.
Explora más sobre nuestro Fabricación de engranajes personalizados capacidades.
Otros artículos que te pueden interesar: