Engrenages ont persisté pendant des siècles, ce qui en fait l'un des éléments mécaniques les plus anciens mais toujours d'actualité aujourd'hui.
Diverses méthodes, dont fonderie, le forgeage, l'extrusion, la métallurgie des poudres, le découpage et le fraisage d'engrenages peuvent être utilisés pour fabriquer des engrenages. Il n’existe pas de processus unique pour la fabrication d’engrenages car ils nécessitent des processus différents selon le type et l’application. Cependant, le processus d'usinage revêt une importance significative pour atteindre la taille, la forme et les caractéristiques ultimes de l'engrenage. finition de surface.
Ce guide explorera la fabrication d'engrenages, couvrant les processus courants, les opérations de post-traitement et les matériaux.

Qu’est-ce que la fabrication d’engrenages ?
Le processus de fabrication des engrenages implique la production et le façonnage précis des engrenages, qui sont des composants essentiels utilisés dans les machines pour transmettre couple. Les engrenages, connus pour leur mouvement de rotation, ont des dents qui s'emboîtent avec celles d'un autre mécanisme denté, permettant un transfert en douceur de la puissance mécanique.
La création d'engrenages est réalisée par diverses méthodes, notamment l'usinage, la métallurgie des poudres, le moulage et l'emboutissage. Le fraisage, le brochage et l'entraidement des engrenages comptent parmi les techniques les plus précises et les plus populaires utilisées pour obtenir des profils d'engrenages complexes et bien définis. Ces méthodes garantissent la fabrication précise des engrenages nécessaires à diverses applications dans les machines.
Divers matériaux, tels que les métaux, les plastiques et même le bois, sont utilisés dans la construction des engrenages. Les progrès technologiques ont permis la formation d'engrenages en métal et en plastique grâce à moulage sous pression ou moulage par injection, proposant des méthodes de fabrication alternatives. Cela permet aux fabricants d’explorer des options allant au-delà de la production traditionnelle d’engrenages. Néanmoins, il est essentiel de reconnaître que certaines situations nécessitent des opérations de post-traitement pour améliorer la qualité du produit final.

Processus typiques de fabrication d'engrenages
Les méthodes de fabrication d'engrenages ont généralement été classées en trois catégories principales : la génération, le formage et la découpe de forme.
- Le formage d'engrenages crée des engrenages sans utiliser d'outils de coupe (c'est-à-dire fonderie, forgeage, métallurgie des poudres, impression 3D)
- La découpe d'engrenages implique des outils utilisés pour créer le profil de l'engrenage (c'est-à-dire fraisage d'engrenages, brochage et EDM).
- La génération d'engrenages utilise des outils de coupe ayant la forme du profil d'engrenage souhaité pour créer l'engrenage (c'est-à-dire façonnage d'engrenages et taillage d'engrenages).
Formation d'engrenages
Fonderie
Le moulage est un processus de mise en forme dans lequel du métal en fusion est versé dans une cavité de moule pour créer des formes. Il s'agit d'un processus relativement simple, principalement utilisé pour produire des ébauches ou des cylindres pour les engrenages, tandis que les dents sont généralement fabriquées par usinage.
Il existe pourtant un domaine spécifique dans lequel la fonderie s’impose comme le mode de fabrication privilégié dans l’industrie : la production d’engrenages de très grandes dimensions. Les méthodes d'usinage et autres techniques de formation d'engrenages sont moins pratiques pour les grands diamètres. En règle générale, les engrenages plus grands sont principalement du type à engrenages droits, ce qui fait du moulage une excellente option en raison de sa relative simplicité.
Moulage de coquilles, moulage sous pression, moulage en sable, et moulage en moule permanent sont les types de méthodes de moulage les plus répandus utilisés pour la production d'engrenages.

Forger
Ce processus offre la flexibilité nécessaire pour produire à la fois des ébauches et des engrenages finis en fonction d'exigences spécifiques. Le forgeage est particulièrement adapté aux engrenages relativement simples.
En théorie, le forgeage est une excellente méthode de fabrication d'engrenages pour les applications lourdes, et ce, pour une raison simple. Le traitement thermique impliqué dans le forgeage conduit à des engrenages présentant des propriétés de fatigue améliorées. Cependant, la force importante requise pour le forgeage limite la taille et la finesse des engrenages produits.
En règle générale, le forgeage est efficace pour les engrenages allant de 6 à 10 pieds de diamètre. En fonction du type de forgeage, tel que le forgeage de précision, l'usinage peut être nécessaire ou non pour le produit final d'engrenage.

La fabrication additive
Fabrication Additive, communément appelée impression en 3D, fonctionne en construisant couche par couche un objet tridimensionnel, basé sur un modèle CAO 3D. Cette approche permet aux machines additives de produire des conceptions complexes, incorporant des structures en treillis conçues pour réduire la masse, un exploit difficilement réalisable avec les méthodes traditionnelles. La création de telles géométries implique souvent l'utilisation de Topologie 3D optimisation et conception informatique générative.
Des procédés de fabrication additive peuvent être utilisés pour fabriquer des engrenages conventionnels et non circulaires. De plus, les imprimantes 3D de haute qualité sont désormais abordables et facilement accessibles.
Métallurgie des poudres
Métallurgie des poudres sert de méthode de formage de haute précision qui présente une alternative rentable aux engrenages traditionnels en acier et en fonte finis à la machine. Cependant, il ne convient pas aux engrenages de plus grande taille et excelle plutôt dans la production de petits engrenages de haute qualité. éperon, biseau, et des engrenages en spirale.
La porosité du matériau résultant dans les engrenages plus grands entraîne une réduction de la fatigue et de la résistance aux chocs, limitant leur capacité portante. Néanmoins, le recours à un procédé de frittage peut améliorer leurs propriétés mécaniques.
Cette méthode s'avère avantageuse pour les conceptions d'engrenages incorporant des caractéristiques telles que des trous, des dépressions et des niveaux de surface ou des projections variables. Malgré ces avantages, le coût initial d’installation de la métallurgie des poudres est considérablement élevé, ce qui la rend peu pratique pour une production en faible volume.

Obturation
Le découpage, similaire à l'extrusion, partage de nombreuses similitudes mais est limité dans ses capacités tridimensionnelles. Cette méthode de formation d'engrenages utilise de la tôle et plusieurs matrices pour obtenir la forme souhaitée. Différents types d'engrenages peuvent être produits à l'aide du processus de découpage, les engrenages droits offrant des résultats optimaux.
À l’heure actuelle, le processus de découpage trouve des applications dans la production d’engrenages dans plusieurs industries, en particulier pour les utilisations légères. Il s'agit notamment des équipements de bureau, des systèmes hydrauliques, des petits appareils médicaux et d'autres applications nécessitant des charges relativement faibles.
Découpe de forme d'engrenage
Fraisage
Le fraisage d'engrenages implique l'utilisation d'un outil de coupe de forme sur un fraiseuse pour sculpter des dents d'engrenage à partir d'une ébauche d'engrenage. Ce processus d'usinage fondamental repose sur le mouvement entre une fraise rotative à plusieurs tranchants et une pièce à usiner pour façonner des dents d'engrenage individuelles.
Bien que la méthode de coupe par fraisage soit quelque peu limitée dans son application, elle excelle dans la production de géométries d'engrenages complexes et peut exécuter des coupes personnalisées sans nécessiter d'outillage spécial.
Le fraisage CNC est couramment utilisé pour fabriquer des roues dentées hélicoïdales et droites pour diverses industries, telles que les transmissions automobiles, ainsi que les fraises-mères.

Brochage
Le brochage s’impose comme l’une des techniques les plus rapides pour la découpe d’engrenages. Il utilise un outil de coupe à plusieurs dents appelé broche, chaque dent étant généralement plus haute que la précédente. Cette variation incrémentielle de hauteur facilite la création de coupes plus petites et plus faciles, donnant rapidement la forme souhaitée sans sacrifier la précision.
Bien que cette méthode de production d’engrenages soit généralement associée aux engrenages internes, elle se prête également à la création de dents externes. Pour ce faire, un outil spécialisé pour «brochage de pot» est utilisé, garantissant une réplication du même niveau de précision et d’efficacité.
Usinage par électroérosion (EDM)
L'EDM représente une technique de fabrication électromécanique dans laquelle la matière est éliminée d'une pièce en évoquant une séquence de décharges de courant entre deux électrodes divisées par un bain liquide diélectrique. Au lieu de couper, l’étincelle sert d’« outil de coupe » qui érode essentiellement le matériau.
L'EDM excelle dans la découpe de géométries complexes de toutes tailles, y compris en tant que processus de taille d'engrenages. Cependant, la méthode a ses inconvénients. L'absence de contrôle et de programmation précis peut entraîner des surfaces de pièces endommagées, ce qui est particulièrement difficile pour les programmes CNC d'exécuter des profils de dents courbes. Néanmoins, l'application de produits de haute qualité et conviviaux modélisation 3D et les logiciels de FAO, tels que Feature CAM, Autodesk Fusion, Master CAM et autres, peuvent faciliter le mouvement fluide nécessaire à la coupe de dents courbes.
Ces dernières années, les machines d'électroérosion ont subi des améliorations, réduisant les problèmes de finition de surface et augmentant la précision de coupe et les propriétés des matériaux qui en résultent (microstructure, propriétés mécaniques, etc.). Ce processus peut atteindre des tolérances serrées aussi infimes que des millièmes de pouce et fabriquer des engrenages à la fois minuscules (avec une fraction de pouce de diamètre) et substantiels (avec un diamètre dépassant 20 pouces). L'EDM est utilisé pour des applications délicates dans les montres et horloges ainsi que pour couper des engrenages robustes, y compris ceux utilisés dans les voitures de course.

Génération d'engrenages
Fraisage des engrenages
Le processus de taillage d'engrenages implique l'utilisation d'un dispositif de coupe conique appelé fraise-mère, la fraise-mère et la pièce tournant à mesure que la fraise-mère tourne autour de l'ébauche d'engrenage.
Les engrenages droits sont principalement produits à l'aide de cette méthode, bien qu'une gamme d'autres engrenages, notamment les engrenages cycloïdes, engrenages hélicoïdaux, engrenages à vis sans fin, cliquets, et pignons, sont tous fabriqués par taillage. La qualité de la table de cuisson est de la plus haute importance, en particulier lors de la découpe de géométries complexes.
Le taillage d'engrenages n'est généralement pas adapté aux engrenages internes. Semblable au façonnage d'engrenages, le taillage offre des avantages de configuration mais est limité aux coupes externes, car la fraise-mère sculpte l'extérieur des ébauches d'engrenages.

Façonnage des engrenages
Le processus de façonnage des engrenages implique une fraise dont le profil correspond à la géométrie des dents souhaitée. Cet outil de coupe utilise un mouvement linéaire pour enlever la matière de l'ébauche d'engrenage, comprenant une course de coupe et de retour. Le pas de l'outil de façonnage d'engrenage s'aligne sur le pas requis pour la dent d'engrenage, s'adaptant aux engrenages avec différentes quantités de dents.
Le façonnage des engrenages s'avère être une solution viable pour les séries de production de taille moyenne, offrant des avantages en termes de vitesse, de conception et de configuration pour la production de masse et facilitant la création de la plupart des types d'engrenages, à l'exception des engrenages à vis sans fin et des engrenages internes. Cependant, l'inconvénient de la mise en forme des engrenages réside dans la rigidité limitée du bras de coupe, ce qui entraîne une précision réduite.
Méthode Sunderland
Parmi les principales techniques de fabrication d'engrenages, les fraises à crémaillère jouent un rôle de premier plan. Le processus de découpe à crémaillère, également appelé méthode Sunderland ou système Sunderland, implique une machine à engrenages équipée d'une fraise à crémaillère présentant des angles de coupe et de dégagement pour façonner les profils de dents sur une ébauche d'engrenage. Cette méthode repose sur le mouvement relatif spécifique entre la pièce à usiner et la fraise pendant l'usinage, semblable à une crémaillère et un pignon.
La méthode Sunderland excelle dans la production de formes de dents uniformes, et les engrenages coupés par la même fraise sont théoriquement capables de s'engrener correctement les uns avec les autres. En conséquence, des conceptions d'engrenages nécessitant une haute précision, notamment des engrenages à double hélice, peuvent être produites efficacement à l'aide de cette méthode. De plus, la méthode Sunderland s'avère polyvalente et rentable, en particulier pour les séries de production moyennes à élevées.
Post-traitement pour la fabrication d'engrenages
Une fois les processus de fabrication des engrenages détaillés ci-dessus terminés, l'état de surface et la précision dimensionnelle des engrenages peuvent ne pas répondre aux exigences spécifiques de certaines applications. Par conséquent, une série d’opérations de finition devient nécessaire. Ces activités de post-traitement englobent une gamme de traitements, notamment le traitement thermique pour améliorer les caractéristiques de fatigue, ainsi que la correction dimensionnelle et la finition de surface.
Voici les cinq procédés de finition de surface les plus couramment utilisés dans la production d'engrenages.
- Meulage : Ce processus de finition de surface bien connu permet d’obtenir efficacement une finition lisse sur toute la surface, comme son nom l’indique. Il peut être exécuté de manière intermittente ou continue sans affecter les résultats.
- Rodage : adapté aux engrenages délicats nécessitant la plus grande précision, le rodage utilise de petites particules abrasives pour lisser méticuleusement une surface à des vitesses faibles ou moyennes.
- Honage : Un autre procédé largement utilisé, l’affûtage polit la surface, lui conférant une texture lisse tout en corrigeant également les erreurs mineures dans la géométrie des dents.
- Rasage : impliquant l'élimination de couches extrêmement fines de la surface pour obtenir un profil lisse, le rasage est un processus relativement coûteux et est rarement utilisé dans la production d'engrenages.
- Brunissage : Cette technique consiste à utiliser la compression pour affiner la surface, essentiellement en la lissant.
Matériaux disponibles pour la fabrication d'engrenages
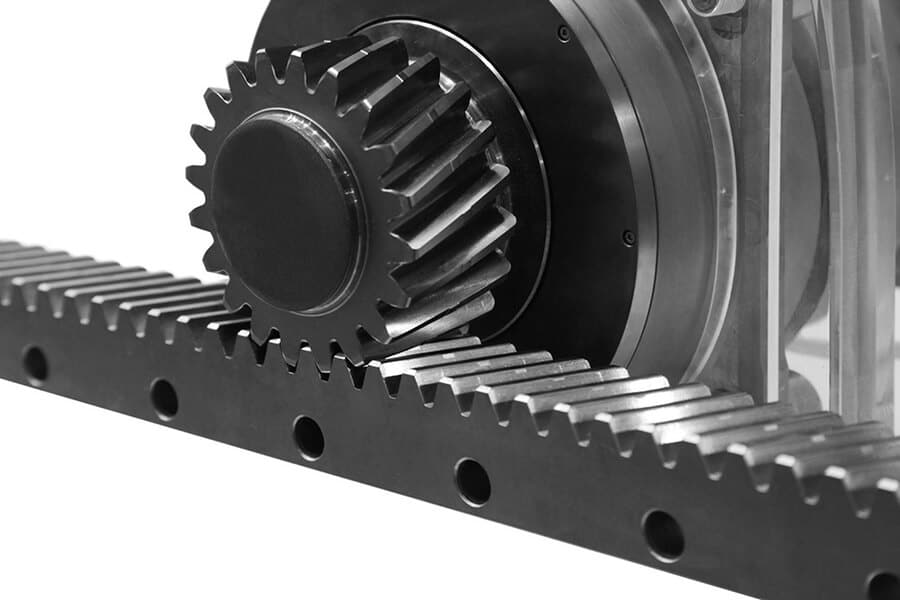
Pour des performances fiables et une durée de vie prolongée, un engrenage doit posséder des caractéristiques spécifiques, notamment :
- Faible coefficient de frottement
- Excellente fabricabilité
- Haute résistance à la traction pour supporter des charges statiques
- Haute endurance pour résister aux variations de charge
De nombreux matériaux sont utilisés dans la production d'engrenages pour conférer ces propriétés critiques. Vous trouverez ci-dessous un aperçu de chaque matériau et de ses atouts distinctifs.
Fonte
La fonte peut supporter une usure répétée et soutenue, ce qui la rend bien adaptée à la fabrication d'engrenages de précision. Le processus de moulage permet de produire facilement des formes d'engrenages complexes. Les engrenages en fonte sont fréquemment utilisés dans les applications où la douceur de fonctionnement n'est pas une préoccupation majeure.
Acier
Les engrenages fabriqués à partir d'alliages d'acier offrent une résistance élevée car ils sont généralement soumis à traitement thermique pour améliorer la ténacité et la dureté, en particulier au niveau des dents. Notamment, Acier Carbone est utilisé dans la production de crémaillères hélicoïdales, droites, coniques, à vis sans fin et à engrenages.
Laiton
Combinaison de cuivre et de zinc, le laiton est un alliage qui permet aux fabricants d’ajuster la teneur en zinc. Le laiton avec de faibles niveaux de zinc offre une plus grande ductilité par rapport aux autres matériaux, et sa base en cuivre rend le métal antimicrobien et facile à usiner. En règle générale, les engrenages en laiton sont utilisés dans des applications à faible charge telles que les engrenages droits ou les crémaillères.
Bronze
Outre le laiton, d'autres alliages de cuivre contiennent également des alliages de bronze d'aluminium et de bronze au phosphore. Ces engrenages non magnétiques sont particulièrement adaptés à une utilisation dans des environnements corrosifs.
Combinant du cuivre, de l'étain et du phosphore, le bronze phosphoreux offre une résistance et une résistance à la corrosion améliorées grâce à la présence d'étain, tandis que l'ajout de phosphore améliore sa rigidité et sa résistance à l'usure. Cela rend les engrenages en bronze phosphoreux bien adaptés aux environnements à friction élevée, en particulier dans les engrenages à vis sans fin, car le matériau résiste efficacement au frottement provoqué par la roue et minimise les effets de la lubrification.
Composé de cuivre, d'aluminium, de nickel, de fer et de manganèse, le bronze d'aluminium présente une résilience exceptionnelle contre l'usure et la corrosion, ce qui en fait un choix privilégié pour une utilisation dans des environnements hautement corrosifs exposés à l'eau salée, à l'oxydation et à la corrosion. acides organiques. De plus, sa capacité à prospérer dans des environnements à forte charge le rend adapté aux applications impliquant des roues à vis sans fin et des engrenages à vis.
Alliages d'aluminium
Dans les environnements qui exigent des engrenages avec un rapport résistance/poids élevé, les alliages d'aluminium constituent un substitut viable aux alliages de fer. De plus, les engrenages fabriqués en alliages d'aluminium bénéficient d'une finition de surface protectrice appelée passivation, les protégeant contre la corrosion et l'oxydation.
Les alliages d'aluminium les plus utilisés dans la fabrication d'engrenages comprennent 2024, 6061, et 7075. Quelle que soit la qualité, les engrenages en aluminium conviennent mieux aux applications à températures faibles à modérées, car ils commencent à se dégrader à environ 400 °F.
Métaux en poudre
Ces métaux sont constitués de diverses combinaisons de matériaux métalliques, notamment de l'acier fer-nickel, de l'acier préallié et des mélanges personnalisés. De plus, leur porosité contribue à un fonctionnement plus silencieux des engrenages et ils peuvent être rendus autolubrifiants grâce à une imprégnation sous vide avec différentes huiles.
Le processus comprend trois étapes clés :
- Développer la combinaison optimale qui correspond aux spécifications de durabilité, de précision et de fiabilité
- Compacter le mélange sous pression contrôlée pour répondre aux exigences exactes
- Chauffage ou frittage du mélange pour obtenir une forme permanente
La métallurgie des poudres est capable de produire des engrenages coniques, coniques en spirale, droits, hélicoïdaux, à pignon et combinés.
Thermoplastiques
Dans la fabrication de précision, les engrenages légers dépendent largement de thermoplastiques. Ces engrenages peuvent être produits de la même manière que les engrenages métalliques, avec moulage par injection étant souvent la méthode privilégiée. L'acétal est un choix populaire parmi les fabricants en raison de sa stabilité sur de larges plages de températures, de faibles coefficient de friction, et la résistance au fluage.
Fournisseur de solutions de fabrication d'engrenages personnalisés – Runsom Precision
Opérer dans le domaine hautement spécialisé de la fabrication d’engrenages exige une précision et une exactitude élevées. En raison de leur rôle crucial dans les systèmes mécaniques, même les imperfections de fabrication les plus mineures peuvent avoir de graves conséquences. Ainsi, il est recommandé de bien choisir votre prestataire de services.
Lorsqu'il s'agit d'usinage d'engrenages de précision, Précision Runsom est prêt à aider. Nous sommes spécialisés dans la fabrication d'engrenages de précision personnalisés en utilisant une gamme de matériaux grâce à notre Service d'usinage CNC. Grâce à nos incroyables capacités de fabrication, la fabrication d’engrenages et de pièces mécaniques devient plus rapide, plus rationalisée et notamment plus efficace. Contactez nos experts dès aujourd'hui pour un devis instantané et démarrez votre prochain projet.
En savoir plus sur notre Fabrication d'engrenages sur mesure capacités.
Autres articles qui pourraient vous intéresser :