Se reconoce que los productos fabricados nunca pueden coincidir exactamente con sus diseños teóricos. El tamaño real del producto a menudo difiere del diseño original previsto. El propósito de Dimensionamiento y tolerancias geométricas (GD&T) es controlar y limitar esta variación.
En GD&T, la tolerancia denominada "Posición" se utiliza comúnmente como guía para los fabricantes de la industria del torneado y fresado CNC. Sin embargo, muchas personas tienden a referirse a este símbolo de GD&T como “Posición Verdadera”. En realidad, según el ASME Y14.5 estándar, el término para este símbolo es simplemente “Posición”. Entonces, ¿cómo se definen estos términos y cómo distinguirlos?
Aquí, cubriremos los fundamentos de la posición y la posición verdadera, la diferencia entre la posición y la posición verdadera, y cómo usar, calcular y medir la posición verdadera.
¿Cuál es el puesto en GD&T?
La posición en GD&T, también conocida como Dimensionamiento y Tolerancia Geométrica, define rangos de variación aceptables para la ubicación de características en una pieza. Esta tolerancia es de gran importancia para controlar la ubicación de características críticas como agujeros, protuberancias, patasy otros elementos geométricos.
La tolerancia de posición consta de dos componentes clave: el valor de tolerancia y la referencia de referencia. El valor de tolerancia representa la desviación máxima permitida de la posición real, mientras que la referencia de referencia sirve como punto, línea o plano utilizado como base para la medición.
La tolerancia de posición se puede aplicar a características bidimensionales y tridimensionales, y a diversas herramientas de medición, como máquinas de medición de coordenadas (CMM), se pueden utilizar escáneres láser o comparadores ópticos para evaluarlo. Estas herramientas ayudan a garantizar que las funciones estén ubicadas correctamente para lograr un funcionamiento y ensamblaje efectivos de las piezas.
¿Qué es la verdadera posición en GD&T?
En GD&T, la posición verdadera se refiere a la coordenada o ubicación precisa que representa la valor nominal de una característica. Ofrece información más detallada sobre la posición y la orientación de la característica en comparación con la tolerancia de posición. La posición verdadera define una zona de tolerancia circular, centrada en la posición verdadera, con un diámetro que representa la desviación máxima permitida de la ubicación prevista. Esta tolerancia posicional se especifica en el marco de control de características.
En el estándar ASME Y14.5, el símbolo en forma de cruz (⌖) se usa para representar la posición, pero ahora también se usa para indicar la posición verdadera en GD&T. El símbolo de posición verdadera se aplica a funciones que requieren un alto nivel de precisión posicional, como orificios, pasadores u otros elementos que necesitan una alineación o acoplamiento preciso con otras piezas. Garantiza que la característica se encuentre dentro de la zona de tolerancia especificada en relación con el dato o punto de referencia.
Comprender la posición y la posición verdadera
Para comprender la distinción entre posición verdadera y tolerancia de posición, imaginemos un escenario en el que se lanzan dardos a una diana. Nuestro objetivo es dar en el centro preciso de la diana, que representa la verdadera posición. Sin embargo, en realidad, es muy poco probable que todos los dardos acierten exactamente en el centro. Entonces surge la pregunta: ¿cuánta desviación del centro exacto se considera aceptable? Esta desviación permitida está definida por la tolerancia de posición.
La Figura 1 ilustra la posición que controla la ubicación del orificio en el centro de una pieza, mientras que la posición verdadera indica la ubicación específica del eje del orificio que está determinada por las dimensiones básicas de estar a 2,5 pulgadas de la parte inferior de la pieza (Característica de referencia). B) y 2,5″ desde el lado izquierdo (Característica de referencia C).
Para definir la tolerancia en esta ubicación, se utiliza el marco de control de características para el agujero. Este marco indica que el orificio tiene una tolerancia de posición basada en el diámetro de 0,005 pulgadas.
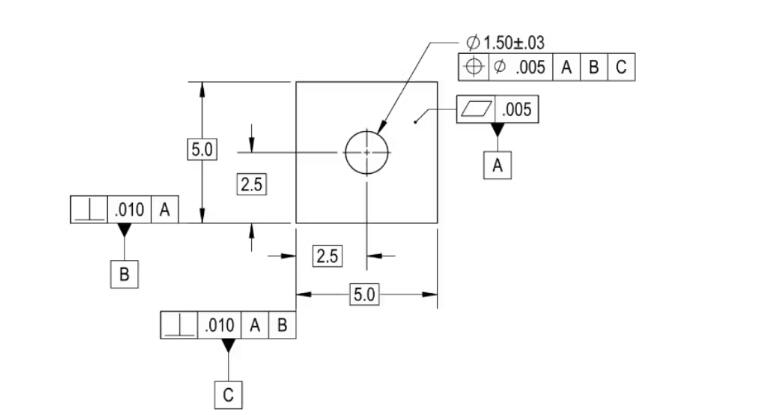
Para comprender mejor el concepto, la figura 2 visualiza la escena del lanzamiento de dardos. Tenga en cuenta que las dimensiones básicas resaltadas en rojo indican la posición real, es decir, llegar exactamente al centro de la diana.
Para representar la tolerancia de posición, podemos ver un anillo azul rodeando la posición real. Imagine esto como el rango aceptable alrededor de la posición real que permite que la característica pase la inspección. En otras palabras, al medir el eje del agujero, éste debe estar dentro de esta zona de tolerancia de posición diametral designada.
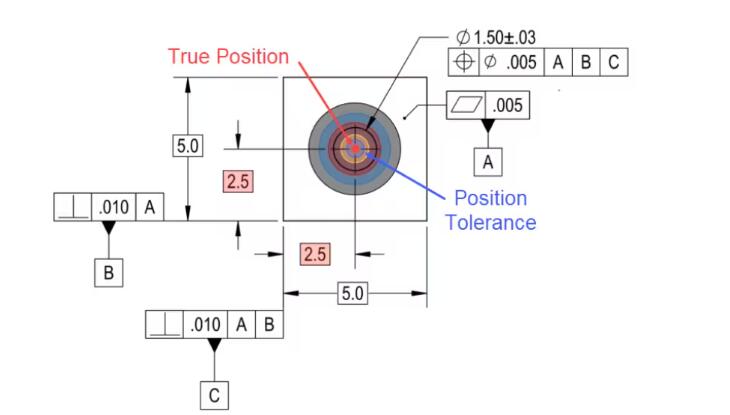
Además, es importante tener en cuenta que no estamos examinando únicamente el eje como una simple ubicación bidimensional. En la Figura 3, se muestra un modelo tridimensional para enfatizar que el eje medido de este orificio debe encajar completamente dentro del área cilíndrica creada por la tolerancia de posición diametral especificada.
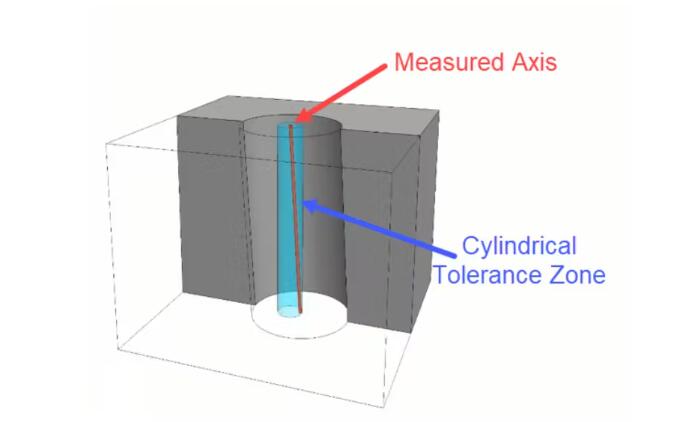
Diferencias entre posición y posición verdadera
La posición verdadera representa la ubicación precisa y especificada de una característica, determinada por dimensiones básicas u otros medios. Por otro lado, la tolerancia de posición define la variación o desviación permitida de la característica de su verdadera posición.
1. Método de cálculo
El cálculo de la tolerancia de posición implica medir la distancia entre la ubicación real de la característica y su ubicación prevista, proyectándola en un plano paralelo al datum especificado.
Por el contrario, el cálculo de la tolerancia de la posición real requiere medir la distancia entre la ubicación real de la característica y su ubicación prevista, proyectándola sobre un cilindro. El diámetro de este cilindro corresponde al valor de tolerancia especificado.
2. Rango de desviación
La tolerancia de posición establece la desviación máxima aceptable de la ubicación de la característica a lo largo de las direcciones X e Y.
Por otro lado, la posición verdadera establece la desviación máxima permitida en cualquier dirección desde la posición verdadera.
3. Referencia de dato
La tolerancia de posición requiere un mínimo de dos referencias de referencia para definir la variación aceptable en la ubicación de la característica.
Por el contrario, la posición verdadera solo requiere una única referencia de referencia para determinar la desviación permitida de la posición verdadera.
4. Complejidad
La posición verdadera suele ser más compleja y difícil de implementar en comparación con la tolerancia de posición. Esta complejidad surge del requisito de calcular variaciones en todas las direcciones desde la posición real.
5. Solicitud
La tolerancia de posición se emplea normalmente cuando la ubicación de una característica tiene importancia, pero su orientación no es de suma importancia.
La verdadera posición entra en juego cuando tanto la ubicación como la orientación del elemento son cruciales.
A continuación, el vídeo proporciona una explicación detallada de la posición real y el control de posición en GD&T.
Características de la Zona de Tolerancia
La zona de tolerancia para la posición verdadera se puede representar de dos formas diferentes, según la leyenda utilizada: cilíndrica y cuadrada.
Zona de tolerancia cilíndrica
En GD&T, el símbolo utilizado para representar la posición verdadera es un símbolo de cruz (⌖). Cuando combinamos este símbolo con un símbolo de diámetro (⌀), indica una zona de tolerancia cilíndrica, que es la representación más utilizada.
Para establecer la posición real según nuestro diseño, normalmente asignamos un dato. En algunos casos, se pueden utilizar varios puntos de referencia para garantizar la ubicación precisa de la característica. Estos puntos de referencia se indican mediante dimensiones básicas.
La posición real sirve como nuestro punto de referencia para medir la desviación de las piezas fabricadas reales. Generalmente se establece en el centro de la característica que se está evaluando. Por ejemplo, en el caso de un agujero, la posición verdadera se establece en el eje del agujero. Alrededor de este eje, definimos una zona de tolerancia de diámetro 2D o 3D según las características de la característica.
Por lo tanto, tenemos un eje de referencia para el agujero en la posición real, y la zona de tolerancia establece el límite dentro del cual el eje de la característica real de la pieza puede variar.
La zona de tolerancia 3D se puede visualizar como un cilindro virtual que abarca el eje del orificio con un diámetro correspondiente al valor de tolerancia especificado. Este cilindro se extiende por todo el espesor de la pieza.
Zona de tolerancia cuadrada
En lugar de utilizar el signo del diámetro, la tolerancia de posición verdadera indica la misma área cuadrada que la tradicional. tolerancia lineal.
Esto da como resultado una zona de tolerancia más estrecha, razón por la cual no se usa comúnmente. El uso de este método de llamada puede resultar en la pérdida de más de 36% de la zona de tolerancia.
¿Cómo aplicar la posición real a una característica?
La posición verdadera es una designación comúnmente utilizada en GD&T. Se utiliza frecuentemente en lugar de concentricidad y simetría, que también forman parte del grupo de control de ubicación de GD&T. La posición verdadera permite un control y una medición más fáciles de las ubicaciones de las características, proporcionando una forma estandarizada de expresar la ubicación y eliminando la confusión.
Para aplicar la posición verdadera a una característica, es importante comprender el concepto de marco de control de características. El marco de control de funciones se compone de tres bloques principales:
- Símbolo de la característica geométrica.
- El valor de tolerancia y cualquier modificador relacionado con la condición del material.
- Planos o ejes de referencia
Supongamos que queremos indicar en nuestro dibujo la posición real y la tolerancia posicional de un agujero ubicado en el centro de una pieza de trabajo con unas dimensiones de 100 x 100 x 50 mm (largo x ancho x alto). El agujero tiene un diámetro de 1 mm con una tolerancia de ±0,005 mm.
Elige el tipo de característica geométrica.
Como indicamos la posición verdadera en el marco de control de características, la representaremos usando el símbolo asignado de la cruz (⌖) en el bloque de símbolos de características geométricas.
Elegir dato
Comenzamos seleccionando el plano de referencia. Podemos utilizar al menos un dato, que puede ser un punto, una recta o un plano.
En este ejemplo, seleccionaremos tres planos de referencia y les asignaremos nombres en orden descendente de importancia.
Nuestro primer dato será el plano inferior de la pieza de trabajo, designado como Dato A. Este dato indica que el eje del agujero debe ser perpendicular a este plano, asegurando el control de la perpendicularidad.
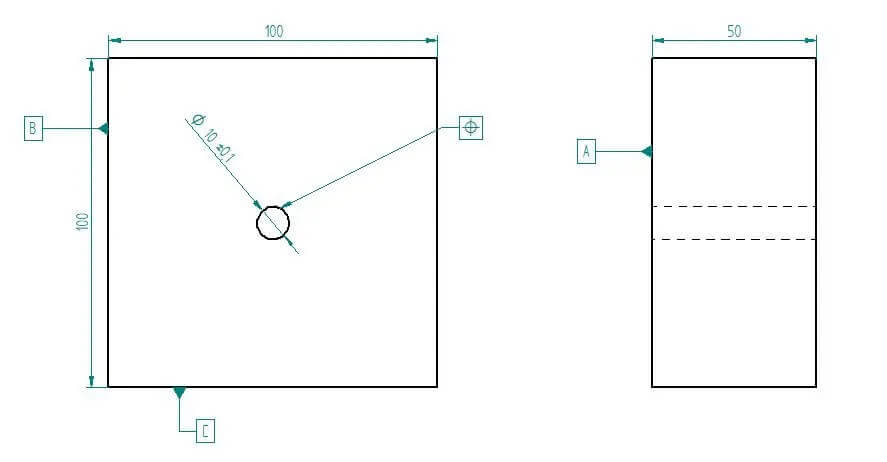
Para el segundo y tercer datum elegiremos los planos de la cara izquierda y frontal respectivamente. Etiquetaremos estos datos como Datum B y Datum C en el plano de ingeniería.
A continuación, especificaremos la distancia de la característica del agujero desde los planos de referencia B y C en el dibujo. En este caso ambas distancias son de 50 mm ya que el agujero se sitúa en el centro. Estas distancias se muestran como dimensiones básicas y están encerradas en un cuadro para transmitir la misma información.
En el marco de control de funciones, escribiremos los Datum A, B y C en los bloques 3, 4 y 5, respectivamente.

Describir la zona de tolerancia y los valores.
En este ejemplo, utilizaremos la zona de tolerancia cilíndrica, que se representará en el marco de control de características mediante el símbolo de diámetro (⌀).
Además, indicaremos el ancho de tolerancia total como 0,01 mm (±0,005 mm).
Modificadores de condición de materiales
Si hay algún modificador relacionado con el condición material, los incluimos después del valor de tolerancia. Una 'M' encerrada en un círculo representa la condición máxima del material (MMC) y una 'L' encerrada en un círculo representa la condición mínima del material (LMC). MMC se utiliza más comúnmente que LMC.

La tolerancia de posición verdadera se utiliza frecuentemente junto con una modificador de condición del material. Las piezas se toleran dentro de estos límites para garantizar que no interfieran excesivamente durante el acoplamiento. Si se produce interferencia, es limitada, incluso cuando las piezas se encuentran en sus límites de tolerancia.
Para un eje, MMC representa el tamaño más grande permitido (diámetro), mientras que para un agujero, representa el tamaño más pequeño permitido. Al asegurarnos de que la MMC del eje sea más pequeña que la MMC del orificio en nuestros diseños, siempre podemos mantener cierta holgura entre los dos.
Cuando incluimos este modificador en nuestro marco de control de posición real, indica que estamos aplicando las tolerancias en función de la condición máxima del material. Esto asegura que el orificio no sea demasiado pequeño o que el eje no sea demasiado grande en ningún punto a lo largo de la profundidad de la característica. Por tanto, con este tipo de control de funciones, podemos controlar no sólo el tamaño y la ubicación sino también la orientación.
¿Cómo calcular la posición real?
La función de posición verdadera tiene múltiples aplicaciones, pero puede resultar un poco compleja cuando se trata de inspección. Comencemos por comprender cómo calcular la posición de una pieza fabricada en relación con la posición real de la característica.
La posición verdadera se determina mediante la siguiente fórmula:
Posición verdadera = 2 x SQRT[(X medido – X verdadero)^2 + (Y medido – Y verdadero)^2]
Dónde,
El valor medido se refiere a la lectura obtenida de los instrumentos de medición.
El valor verdadero representa la posición verdadera indicada por las dimensiones básicas
Estos cálculos se pueden realizar mediante una calculadora sencilla o mediante cálculo manual, ya que básicamente se trata de duplicar el valor de la hipotenusa obtenido al aplicar la Teorema de pitágoras.
Formas de medir la posición real
Si el valor calculado cae dentro del rango especificado, consideramos que la pieza es aceptable. Hay varios métodos disponibles para realizar estas mediciones. Exploremos estas opciones.
1. Máquina de medición de coordenadas (MMC)
máquinas CNC en talleres mecánicos Por lo general, están equipados con una CMM que proporciona mediciones de alta precisión. Estas CMM miden digitalmente las piezas y realizan todos los cálculos.
La CMM se considera el método más preciso para medir la posición real. Consiste en un brazo robótico con una bola al final. Maniobramos la pelota hasta la característica específica que queremos medir. Luego, la CMM rastrea la característica y convierte el movimiento en el perfil de la característica utilizando un software especializado.
El proceso de medición puede ser algo complejo. Para ayudarle con esto, hemos descrito una serie de pasos generales que pueden resultar útiles. Cuando utilizamos una CMM, normalmente seguimos estos pasos para realizar la medición:
Determina tu dato
Consulte la impresión para identificar y localizar el dato especificado. Por ejemplo, supongamos que el Datum A es una superficie de referencia, el Datum B es un eje de referencia y el Datum C es un origen de referencia.
Alinear la pieza
Asegúrese de que el avión esté nivelado y ajústelo en consecuencia. Gire la pieza para alinearla con la línea designada y establezca el punto de origen como referencia C.
Medir características
Identifique la dimensión que indica la posición real y mídala.
Posición de dimensión
Comience haciendo clic en "Dimensión" y elija la opción "Posición". Luego, procede a denunciarlo.
Si está utilizando marcos de control de características, es necesario definir el dato en el editor antes de seleccionar las características que desea informar.
2. Calibrador especial
Podemos utilizar un conjunto especializado de calibradores llamado calibrador digital de distancia central para medir la posición. Este tipo de calibrador puede determinar la distancia central entre dos orificios o orificios escalonados. Es capaz de medir varios tamaños de centros de orificios.
Este calibrador se puede utilizar tanto para mediciones escalonadas como externas. Está diseñado con características fáciles de usar, como mecanismos de bloqueo, capacidades de ajuste fino y funciones de preajuste de datos.
3. Indicador funcional fijo
Este método suele considerarse la forma más rápida de medir la posición real. Se utiliza comúnmente en procesos de fabricación de gran volumen debido a su eficiencia. Un medidor funcional está diseñado específicamente para medir la posición y no el tamaño de la característica.
Por ejemplo, al medir la posición real de un orificio en una pieza de trabajo: el medidor funcional consiste en un bloque con un pasador que sobresale colocado en la posición real del orificio. El medidor también incluye otras características que se alinean con el datum. Si el pasador puede entrar en el orificio cuando el calibre está alineado con el punto de referencia, se acepta la pieza. Sin embargo, tenga en cuenta que la medición del tamaño de la característica debe realizarse por separado.
Conclusión
En resumen, la posición verdadera representa la ubicación precisa de una característica basada en dimensiones básicas, mientras que el símbolo de posición denota la tolerancia posicional, que es la cantidad aceptable de desviación de esa característica de su posición verdadera.
Servicios de mecanizado CNC de precisión personalizados – Runsom Precision
El mecanizado de piezas no es una tarea que se pueda encomendar a cualquiera. Necesita expertos experimentados que tengan amplios conocimientos en la industria manufacturera. Es por eso que Precisión Runsom es la opción ideal para sus necesidades.
Nuestras sólidas capacidades de fabricación y estrictas medidas de control de calidad garantizan que cumplamos con los requisitos de alta tolerancia de los clientes en diversas industrias. Además, realizamos una inspección dimensional exhaustiva antes de entregar el producto final.
Entendemos que usted valora la eficiencia, por eso ofrecemos cotizaciones instantáneas y plazos de entrega rápidos. En Runsom Precision, nos esforzamos por brindar la mejor solución a un precio razonable que supere sus expectativas. Pedido una cotización instantánea hoy para comenzar con su proyecto hoy.
Otros artículos que te pueden interesar: